High-strength low-alloy steel submerged-arc welding seam capping bead welding method
A low-alloy steel, welding method technology, applied in welding equipment, welding accessories, arc welding equipment, etc., can solve the problems of unrefinement of grains, obvious tendency of cold cracks and reheat cracks, and reheat cracks. , to achieve the effect of optimizing tissue performance
- Summary
- Abstract
- Description
- Claims
- Application Information
AI Technical Summary
Problems solved by technology
Method used
Image
Examples
Embodiment
[0032] The present invention is described in detail by taking the circular seam welding of a voltage stabilizer cylinder of a certain nuclear power unit as an example.
[0033] The material of the base material of the voltage stabilizer cylinder is 16MND5, and the thickness is 114mm. The groove of the circular seam is shown in the attached drawing, and it is welded by the welding method of the present invention. The specific welding process steps are as follows:
[0034] (1) Use manual electrode arc welding to weld the weld number 1, and assemble the base metal of the regulator cylinder;
[0035] (2) Use submerged arc welding to weld the weld number 2, fill the inner groove of the welding, the welding wire specification is φ4.0, and the current is 560A;
[0036] (3) Submerged arc welding is used to weld the cover surface of number 3 on the inner side and the tempering weld bead on this side, the welding wire specification is φ4.0, and the current is 530A;
[0037] (4) Grindin...
PUM
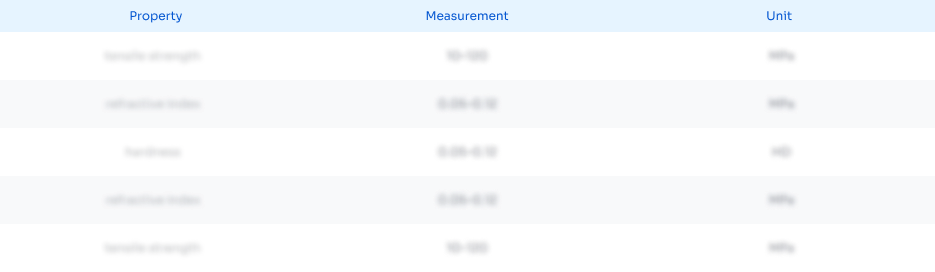
Abstract
Description
Claims
Application Information

- Generate Ideas
- Intellectual Property
- Life Sciences
- Materials
- Tech Scout
- Unparalleled Data Quality
- Higher Quality Content
- 60% Fewer Hallucinations
Browse by: Latest US Patents, China's latest patents, Technical Efficacy Thesaurus, Application Domain, Technology Topic, Popular Technical Reports.
© 2025 PatSnap. All rights reserved.Legal|Privacy policy|Modern Slavery Act Transparency Statement|Sitemap|About US| Contact US: help@patsnap.com