Detection method for checking air leakage of non-oxidation heat treatment furnace radiant tube
A technology of non-oxidation heat treatment and heat treatment furnace, which is applied in the direction of heat treatment equipment, heat treatment process control, and detection of fluid appearance at the leakage point, etc., which can solve the problems of large restrictive conditions for investigation, large equipment damage, and great difficulty, so as to save trouble Low labor cost, no damage to equipment, and less restrictive conditions
- Summary
- Abstract
- Description
- Claims
- Application Information
AI Technical Summary
Problems solved by technology
Method used
Examples
Embodiment Construction
[0025] In order to make the purpose and technical solutions of the embodiments of the present invention more clear, the technical solutions of the embodiments of the present invention are clearly and completely described. Apparently, the described embodiments are some, not all, embodiments of the present invention. Based on the described embodiments of the present invention, all other embodiments obtained by persons of ordinary skill in the art without creative efforts shall fall within the protection scope of the present invention.
[0026] A detection method for checking air leakage in a radiant tube of a non-oxidation heat treatment furnace, the detection steps are as follows:
[0027] Step 1. The heat treatment furnace is in the ignition state, and the burners in each area of the heat treatment furnace are turned off; the guarantee conditions for troubleshooting the radiant tube are 1. The heat treatment furnace is in the ignition state; 2. The residual oxygen analyzer i...
PUM
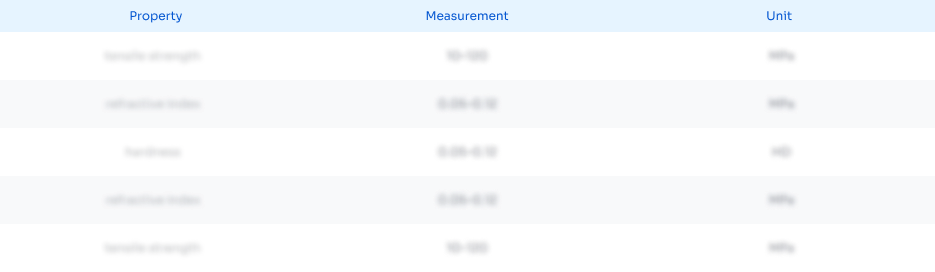
Abstract
Description
Claims
Application Information

- R&D
- Intellectual Property
- Life Sciences
- Materials
- Tech Scout
- Unparalleled Data Quality
- Higher Quality Content
- 60% Fewer Hallucinations
Browse by: Latest US Patents, China's latest patents, Technical Efficacy Thesaurus, Application Domain, Technology Topic, Popular Technical Reports.
© 2025 PatSnap. All rights reserved.Legal|Privacy policy|Modern Slavery Act Transparency Statement|Sitemap|About US| Contact US: help@patsnap.com