Punch forming system for manufacturing metal plate panel of electrical control cabinet
A technology for electrical control cabinets and sheet metal panels is applied in the field of stamping and forming systems for the manufacture of sheet metal panels of electrical control cabinets. , The effect of reducing the hidden danger of scrapping and reducing the number of stampings
- Summary
- Abstract
- Description
- Claims
- Application Information
AI Technical Summary
Problems solved by technology
Method used
Image
Examples
Embodiment Construction
[0028] In order to make the technical means realized by the present invention, creative features, goals and effects easy to understand, the following combination Figure 1 to Figure 8 , to further elaborate the present invention.
[0029] A stamping and forming system for manufacturing electric control cabinet sheet metal panels includes a mounting frame 1, a stamping device 2, a supporting device 3 and a transmission device 4, and the mounting frame 1 is provided with a stamping device 2 and a supporting device 3 sequentially from top to bottom, and the supporting device 3 The outer end is provided with a transmission device 4, and the transmission device 4 is installed on the mounting frame 1, wherein:
[0030] The stamping device 2 includes a hydraulic cylinder A, a connecting plate 21, a connecting rod 22, a forming pressing plate 23, an edge pushing mechanism 24, a connecting column A25, a pressing plate 26, a pre-bending mechanism 27 and a top edge mechanism 28, and the ...
PUM
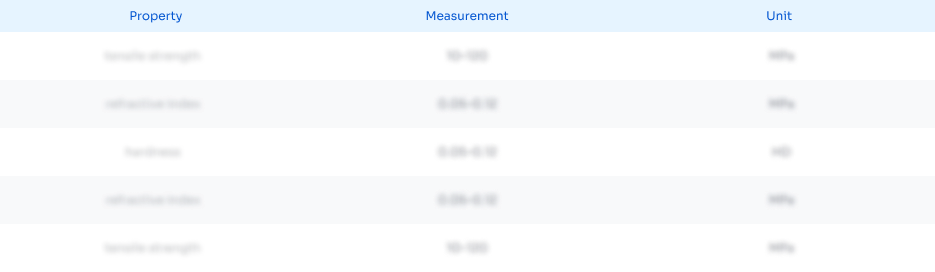
Abstract
Description
Claims
Application Information

- Generate Ideas
- Intellectual Property
- Life Sciences
- Materials
- Tech Scout
- Unparalleled Data Quality
- Higher Quality Content
- 60% Fewer Hallucinations
Browse by: Latest US Patents, China's latest patents, Technical Efficacy Thesaurus, Application Domain, Technology Topic, Popular Technical Reports.
© 2025 PatSnap. All rights reserved.Legal|Privacy policy|Modern Slavery Act Transparency Statement|Sitemap|About US| Contact US: help@patsnap.com