Laser welding method for variable-thickness part
A technology of laser welding and variable thickness, which is applied in the direction of laser welding equipment, welding equipment, welding/welding/cutting items, etc., to ensure the quality of weld seams, avoid laser welding defects, and improve production efficiency and pass rate.
- Summary
- Abstract
- Description
- Claims
- Application Information
AI Technical Summary
Problems solved by technology
Method used
Image
Examples
Embodiment
[0046] see Figure 4 , in this embodiment, the variable thickness parts are described by taking TC4 titanium alloy superplastic forming / diffusion bonding parts as an example, and the thickness changes are as follows Figure 4 As shown, based on the digital model of the part, the data of the welding edge is extracted as follows: A 0 A 1 The length of the welded side of the segment is 0.2m, the thickness is 2mm, A 1 A 2 Segment length is 0.05m, thickness is 1mm, A 2 A 3 Segment length is 0.06m, thickness is 2mm, A 3 A 4 Segment length is 0.06m, thickness is 1mm, A 4 A 5 The segment length is 1.2 m and the thickness is 2 mm.
[0047] It should be further clarified that the laser used in the laser welding method in this embodiment is a high-power fiber laser, YAG laser or disk laser.
[0048] Specifically, in this embodiment, the laser welding method uses argon or helium as the welding shielding gas. It can be understood that, in other embodiments, the welding shielding...
PUM
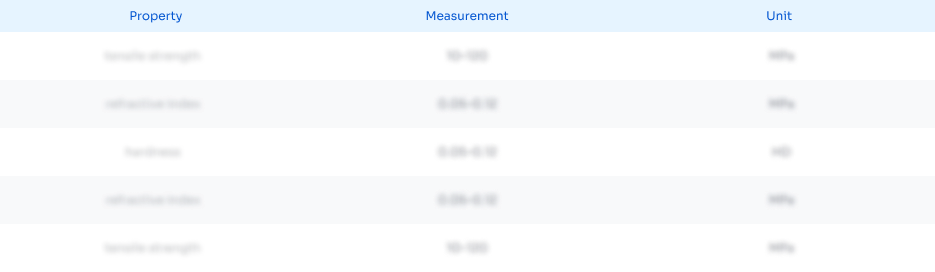
Abstract
Description
Claims
Application Information

- Generate Ideas
- Intellectual Property
- Life Sciences
- Materials
- Tech Scout
- Unparalleled Data Quality
- Higher Quality Content
- 60% Fewer Hallucinations
Browse by: Latest US Patents, China's latest patents, Technical Efficacy Thesaurus, Application Domain, Technology Topic, Popular Technical Reports.
© 2025 PatSnap. All rights reserved.Legal|Privacy policy|Modern Slavery Act Transparency Statement|Sitemap|About US| Contact US: help@patsnap.com