Method for treating waste cutting fluid
A waste cutting fluid and waste water technology, applied in filtration treatment, multi-stage water treatment, water/sewage treatment, etc., can solve the problems of sharp material damage on the film surface, secondary pollution, long treatment time, etc.
- Summary
- Abstract
- Description
- Claims
- Application Information
AI Technical Summary
Problems solved by technology
Method used
Image
Examples
Embodiment Construction
[0090] The technical solutions in the embodiments of the present invention are clearly and completely described below in conjunction with the drawings in the embodiments of the present invention. In the following description, a lot of specific details are set forth in order to fully understand the present invention, but the present invention can also be implemented in other ways different from those described here, and those skilled in the art can do it without departing from the meaning of the present invention. By analogy, the present invention is therefore not limited to the specific examples disclosed below.
[0091] see figure 1 , figure 2 , is an embodiment of a method for treating waste cutting fluid in the present invention, the method includes a waste cutting fluid deslagging and demulsification step 10, a gravity oil-water separation step 20, a waste oil dehydration step 30, a wastewater treatment Step 40, the waste cutting fluid deslagging and demulsification st...
PUM
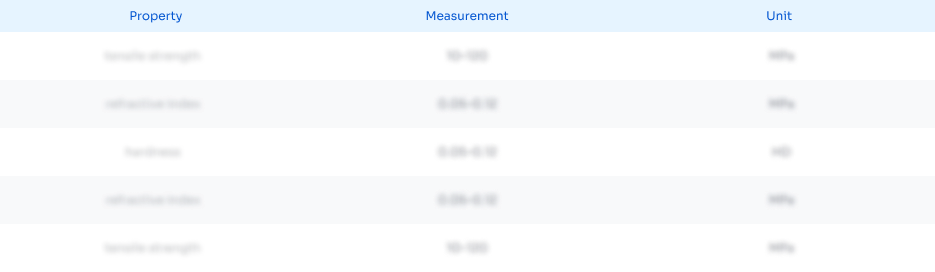
Abstract
Description
Claims
Application Information

- Generate Ideas
- Intellectual Property
- Life Sciences
- Materials
- Tech Scout
- Unparalleled Data Quality
- Higher Quality Content
- 60% Fewer Hallucinations
Browse by: Latest US Patents, China's latest patents, Technical Efficacy Thesaurus, Application Domain, Technology Topic, Popular Technical Reports.
© 2025 PatSnap. All rights reserved.Legal|Privacy policy|Modern Slavery Act Transparency Statement|Sitemap|About US| Contact US: help@patsnap.com