Spiral bevel gear tooth surface Ease-off modification design method based on minimum meshing impact
A technology of spiral bevel gear and design method, which is applied in the field of gear transmission and can solve problems such as inability to achieve
- Summary
- Abstract
- Description
- Claims
- Application Information
AI Technical Summary
Problems solved by technology
Method used
Image
Examples
Embodiment Construction
[0083] The hypoid gear processed by the HFT method is taken as an example below, and the present invention will be further described in conjunction with the accompanying drawings.
[0084] Such as Figure 8 As shown, a kind of spiral bevel gear tooth surface Ease-off modification design method based on the minimum meshing impact provided by the present invention comprises the following steps:
[0085] Step 1: The expression of the tooth surface of the pinion gear that is completely conjugate to the bull wheel. When the tooth surface of the small wheel meshes with the tooth surface of the large wheel, it is completely conjugate, and the transmission ratio is equal to the nominal transmission ratio of the gear pair, so the meshing rotation angle of the large wheel θ 2 Angle of meshing with the small wheel θ 1Relationship:
[0086] θ 2 =z 1 / z 2 (θ 1 -θ 10 )+θ 20 (1)
[0087] where θ 10 , θ 20 is the meshing rotation angle of the large and small wheels at the design ...
PUM
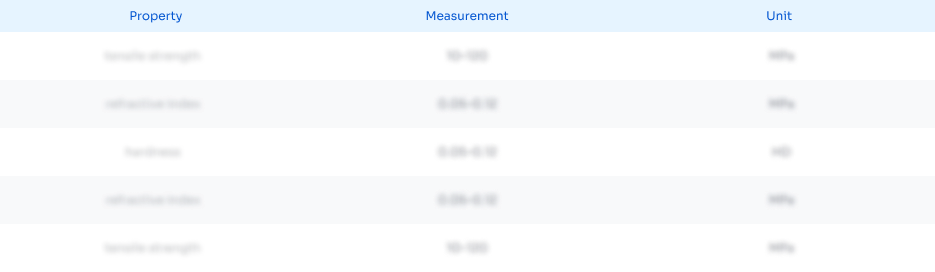
Abstract
Description
Claims
Application Information

- R&D Engineer
- R&D Manager
- IP Professional
- Industry Leading Data Capabilities
- Powerful AI technology
- Patent DNA Extraction
Browse by: Latest US Patents, China's latest patents, Technical Efficacy Thesaurus, Application Domain, Technology Topic, Popular Technical Reports.
© 2024 PatSnap. All rights reserved.Legal|Privacy policy|Modern Slavery Act Transparency Statement|Sitemap|About US| Contact US: help@patsnap.com