Friction wear device
A technology for friction and wear and generating devices, applied in measuring devices, testing wear resistance, instruments, etc., can solve problems such as failure to reach the target order of magnitude, failure to achieve fretting displacement, and difficulty in controlling positive pressure, achieving low cost , improve accuracy, eliminate the effect of force imbalance
- Summary
- Abstract
- Description
- Claims
- Application Information
AI Technical Summary
Problems solved by technology
Method used
Image
Examples
Embodiment Construction
[0029] The present invention is further described below in conjunction with specific embodiment, but protection scope of the present invention is not limited thereto:
[0030] Referring to the accompanying drawings, a high-precision micro-motion displacement generation device includes a micro-motion displacement generation device 1, a laser distance measurement and resultant force measurement device 2, a displacement transmission device 3, a sample clamp device 4, a control and data acquisition device 5 and a positive pressure Applicator 6;
[0031] Described displacement conduction device comprises: the first support plate 301 of three parallel arrangements, the second support plate 302 and the 3rd support plate 303, the length of the first support plate 301 is greater than the length of the second support plate 302, the second support plate The length of 302 is greater than the length of the third support plate 303; the first support plate 301 is horizontally arranged on the...
PUM
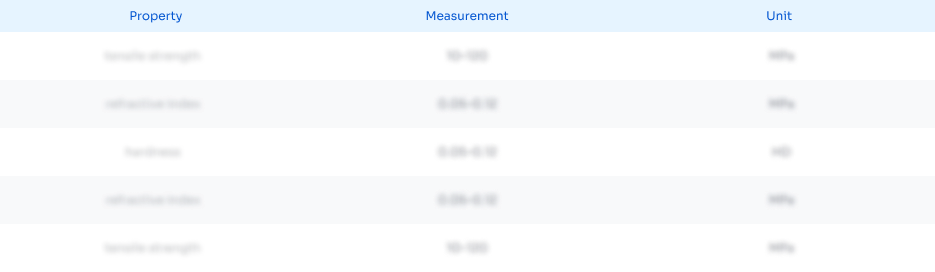
Abstract
Description
Claims
Application Information

- Generate Ideas
- Intellectual Property
- Life Sciences
- Materials
- Tech Scout
- Unparalleled Data Quality
- Higher Quality Content
- 60% Fewer Hallucinations
Browse by: Latest US Patents, China's latest patents, Technical Efficacy Thesaurus, Application Domain, Technology Topic, Popular Technical Reports.
© 2025 PatSnap. All rights reserved.Legal|Privacy policy|Modern Slavery Act Transparency Statement|Sitemap|About US| Contact US: help@patsnap.com