Anti-crease gray fabric finishing process
A process and gray cloth technology, which is applied in the field of anti-wrinkle gray cloth finishing technology, can solve the problems of high cost, high processing cost, high energy consumption, etc., and achieve the effects of improved anti-wrinkle performance, low operating cost, and high film resistance
- Summary
- Abstract
- Description
- Claims
- Application Information
AI Technical Summary
Problems solved by technology
Method used
Examples
Embodiment 1
[0024] The invention provides a wrinkle-resistant gray cloth finishing process, which includes the following process steps: gray cloth singeing→water washing→cold stacking→water washing→oxygen bleaching→dyeing→color fixing→water washing→drying; wherein the cold stacking process adopts deboiling Enzyme auxiliary agent; the scouring enzyme auxiliary agent is used in the oxygen bleaching process, and the color fixing process is to use glacial acetic acid to adjust the pH value of the dyeing bath to 5.6-6, and then remove the fixed color of the cotton gray cloth after color fixing agent treatment, the treatment temperature is controlled at 111-115°C, and the treatment time is 30-40 minutes; the cold batch process refers to rolling the descaling enzyme additive at a controlled water temperature of 50-60°C, and the liquid rolling rate is 90-100% , two rolls and two dips, while the fabric is coiled and rotated on the A-frame, 8 rpm, and stacked at room temperature for 20-24 hours; the...
Embodiment 2
[0040] The invention provides a wrinkle-resistant gray cloth finishing process, which includes the following process steps: gray cloth singeing→water washing→cold stacking→water washing→oxygen bleaching→dyeing→color fixing→water washing→drying; wherein the cold stacking process adopts deboiling Enzyme auxiliary agent; the scouring enzyme auxiliary agent is used in the oxygen bleaching process, and the color fixing process is to use glacial acetic acid to adjust the pH value of the dyeing bath to 5.6-6, and then remove the fixed color of the cotton gray cloth after color fixing agent treatment, the treatment temperature is controlled at 111-115°C, and the treatment time is 30-40 minutes; the cold batch process refers to rolling the descaling enzyme additive at a controlled water temperature of 50-60°C, and the liquid rolling rate is 90-100% , two rolls and two dips, while the fabric is coiled and rotated on the A-frame, 8 rpm, and stacked at room temperature for 20-24 hours; the...
Embodiment 3
[0056] The invention provides a wrinkle-resistant gray cloth finishing process, which includes the following process steps: gray cloth singeing→water washing→cold stacking→water washing→oxygen bleaching→dyeing→color fixing→water washing→drying; wherein the cold stacking process adopts deboiling Enzyme auxiliary agent; the scouring enzyme auxiliary agent is used in the oxygen bleaching process, and the color fixing process is to use glacial acetic acid to adjust the pH value of the dyeing bath to 5.6-6, and then remove the fixed color of the cotton gray cloth after color fixing agent treatment, the treatment temperature is controlled at 111-115°C, and the treatment time is 30-40 minutes; the cold batch process refers to rolling the descaling enzyme additive at a controlled water temperature of 50-60°C, and the liquid rolling rate is 90-100% , two rolls and two dips, while the fabric is coiled and rotated on the A-frame, 8 rpm, and stacked at room temperature for 20-24 hours; the...
PUM
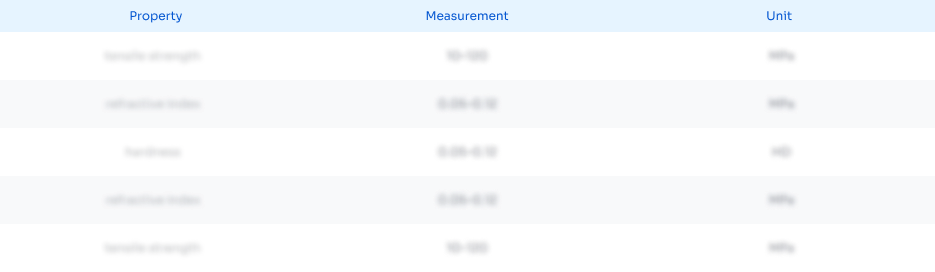
Abstract
Description
Claims
Application Information

- R&D
- Intellectual Property
- Life Sciences
- Materials
- Tech Scout
- Unparalleled Data Quality
- Higher Quality Content
- 60% Fewer Hallucinations
Browse by: Latest US Patents, China's latest patents, Technical Efficacy Thesaurus, Application Domain, Technology Topic, Popular Technical Reports.
© 2025 PatSnap. All rights reserved.Legal|Privacy policy|Modern Slavery Act Transparency Statement|Sitemap|About US| Contact US: help@patsnap.com