A plastic handle positioning and feeding device and a bronzing machine using the device
A feeding device and handle technology, which is applied to conveyors, rotary conveyors, printing machines, etc., to achieve the effect of increasing the degree of automation, reducing labor intensity and improving the efficiency of automatic operation
- Summary
- Abstract
- Description
- Claims
- Application Information
AI Technical Summary
Problems solved by technology
Method used
Image
Examples
Embodiment 1
[0026] like figure 1 , figure 2 , Figure 4 to Figure 6As shown, a plastic handle positioning and feeding device is used for hot stamping machines with screwdriver plastic handles. The plastic handle positioning and feeding device includes an intermittently moving split turntable 1, a workpiece support 2 and a discharge chuck 3. There are six workpiece supports 2 and they are radially distributed on the split turntable 1. The split turntable 1 Every turn 60 ° pauses 0.8 seconds, promptly divides turntable 1 to have six intermittent pause points. Set the intermittent pause point corresponding to the loading position as position 1, clockwise, followed by position 2, position 3, position 4, position 5 and position 6, the discharge position In position six. The unloading chuck 3 is connected to a reciprocating mechanism located next to the dividing turntable 1. The unloading chuck 3 corresponds to the discharge position of the dividing turntable 1, that is, the sixth position...
Embodiment 2
[0030] like image 3 As shown, the rotation drive mechanism includes a rotation drive motor 8, the rotation drive motor 8 is located at the center of the top of the split turntable 1, and is fixed to the top of each substrate mounting seat 15, the output end of the rotation drive motor 8 is provided with a driving bevel gear, and the workpiece support body A bevel gear 6 is fixed at the inner end of the base body 4 , and the bevel gear is driven to mesh with the bevel gear 6 . The bottom end of the center shaft of the dividing turntable 1 is fixedly connected with the output end of a geared motor. All the other are with embodiment 1.
[0031] Through program setting, every time the split turntable 1 rotates one step, that is, the angle of 60°, the rotation drive motor also drives the bevel gear 6 to rotate 60° by driving the bevel gear, so that the workpiece support base 4 and even the workpiece 16 on it rotate 60° by itself. .
Embodiment 3
[0033] There are eight workpiece supports 2, and the dividing turntable 1 has eight intermittent pause points, which are set as positions 1 to 8, the loading position is at position 1, and the unloading position is at position 8. There are two hot stamping devices, corresponding to the third position and the seventh position of the divided turntable 1, which can complete double-sided hot stamping. All the other are with embodiment 2.
[0034] Through the program setting, every time the split turntable 1 rotates one step, that is, at an angle of 45°, the rotation drive motor also drives the bevel gear 6 to rotate 45° by driving the bevel gear, so that the workpiece support base 4 and even the workpiece 16 on it rotate 45°. .
PUM
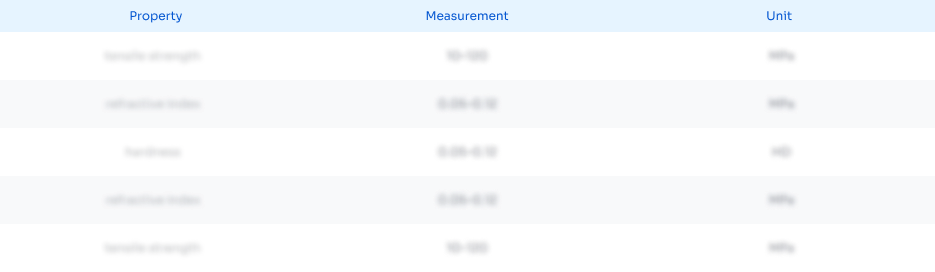
Abstract
Description
Claims
Application Information

- R&D
- Intellectual Property
- Life Sciences
- Materials
- Tech Scout
- Unparalleled Data Quality
- Higher Quality Content
- 60% Fewer Hallucinations
Browse by: Latest US Patents, China's latest patents, Technical Efficacy Thesaurus, Application Domain, Technology Topic, Popular Technical Reports.
© 2025 PatSnap. All rights reserved.Legal|Privacy policy|Modern Slavery Act Transparency Statement|Sitemap|About US| Contact US: help@patsnap.com