Beneficiation method for recovering wolframite from tailings
A mineral processing method and wolframite technology, which is applied in the mineral processing field of recycling wolframite, can solve problems such as difficult to achieve safety and environmental protection, environmental pollution, pipeline and equipment corrosion, and achieve the effect of reducing operating costs and avoiding environmental pollution
- Summary
- Abstract
- Description
- Claims
- Application Information
AI Technical Summary
Problems solved by technology
Method used
Image
Examples
Embodiment 1
[0028] Described method comprises the following steps:
[0029] (1) Grinding wolframite tailings to -0.075mm content is 70%;
[0030] (2) Under the magnetic field intensity of 0.1T, carry out magnetic separation to step (1) gain, obtain weak magnetic concentrate and weak magnetic tailings;
[0031] (3) under the magnetic field intensity of 0.8T, carry out magnetic separation to the weak magnetic tailings gained in step (2), obtain strong magnetic concentrate and non-magnetic tailings;
[0032] (4) classifying the strong magnetic concentrate obtained in step (3), being divided into two grades of +0.0515mm and -0.051mm, and getting the coarse grade wherein;
[0033] (5) carry out re-election to step (4) gain, during re-election, first carry out rough selection, obtain rough selection concentrate, rough selection ore and rough selection tailings, when sweeping, the selected raw material is rough selection, Obtain the scavenging concentrate and scavenging tailings, combine the r...
Embodiment 2
[0041] Described method comprises the following steps:
[0042] (1) Grinding wolframite tailings to -0.075mm content is 80%;
[0043] (2) Under the magnetic field intensity of 0.15T, carry out magnetic separation to step (1) gain, obtain weak magnetic concentrate and weak magnetic tailings;
[0044] (3) Under the magnetic field intensity of 1.1T, carry out magnetic separation to the weak magnetic tailings gained in step (2), obtain strong magnetic concentrate and non-magnetic tailings;
[0045](4) classify the strong magnetic concentrate obtained in step (3), and divide it into two grades of +0.051~0.075mm and -0.051~-0.075mm, and get the coarse grade;
[0046] (5) carry out re-election to step (4) gain, during re-election, first carry out rough selection, obtain rough selection concentrate, rough selection ore and rough selection tailings, when sweeping, the selected raw material is rough selection, Obtain the scavenging concentrate and scavenging tailings, combine the roug...
Embodiment 3
[0054] Described method comprises the following steps:
[0055] (1) Grinding the wolframite tailings until the content of -0.075mm is 90%;
[0056] (2) Under the magnetic field intensity of 0.2T, carry out magnetic separation to step (1) gain, obtain weak magnetic concentrate and weak magnetic tailings;
[0057] (3) Under the magnetic field strength of 1.4T, carry out magnetic separation to the weak magnetic tailings gained in step (2), obtain strong magnetic concentrates and non-magnetic tailings;
[0058] (4) classifying the strong magnetic concentrate obtained in step (3), being divided into two grades of +0.075mm and -0.075mm, and getting the coarse grade wherein;
[0059] (5) carry out re-election to step (4) gain, during re-election, first carry out rough selection, obtain rough selection concentrate, rough selection ore and rough selection tailings, when sweeping, the selected raw material is rough selection, Obtain the scavenging concentrate and scavenging tailings, ...
PUM
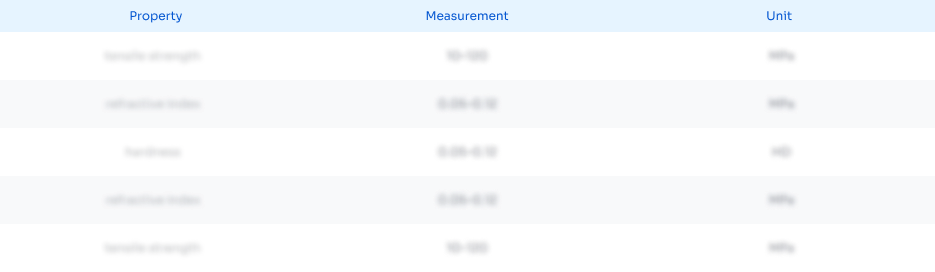
Abstract
Description
Claims
Application Information

- R&D
- Intellectual Property
- Life Sciences
- Materials
- Tech Scout
- Unparalleled Data Quality
- Higher Quality Content
- 60% Fewer Hallucinations
Browse by: Latest US Patents, China's latest patents, Technical Efficacy Thesaurus, Application Domain, Technology Topic, Popular Technical Reports.
© 2025 PatSnap. All rights reserved.Legal|Privacy policy|Modern Slavery Act Transparency Statement|Sitemap|About US| Contact US: help@patsnap.com