Fully assembled high-rise/super high-rise concrete frame-supported structure system and its construction method
A concrete and fully assembled technology, applied in pillars, building components, building structures, etc., can solve problems such as difficulty in meeting the stress requirements of high-rise and super high-rise buildings, lack of reliable detection methods for construction quality, and complex node construction technology. Achieve the effect of convenient and quick connection, improve the fire prevention and corrosion of steel, and improve the overall stability
- Summary
- Abstract
- Description
- Claims
- Application Information
AI Technical Summary
Problems solved by technology
Method used
Image
Examples
Embodiment Construction
[0035] The concrete frame support system of this high-rise / super high-rise building disclosed by the present invention, each floor corresponds to a system unit, and the system unit has two structures:
[0036] The first type of structure mainly includes prefabricated columns, prefabricated wall panels and prefabricated laminated floors. Anchored between. The prefabricated columns of the upper and lower system units are connected through steel structure connectors, and the prefabricated wall panels are connected through grouting.
[0037] Another type of system unit also includes prefabricated laminated secondary beams on the basis of the former system unit structure, and the two ends of the prefabricated laminated secondary beams are connected and fixed with prefabricated columns or prefabricated wall panels according to design requirements.
[0038] preferred embodiment, such as figure 1 , figure 2 As shown, the system unit of this embodiment is the aforementioned first s...
PUM
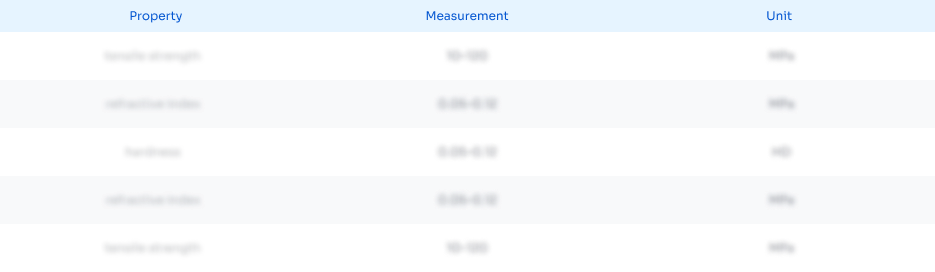
Abstract
Description
Claims
Application Information

- R&D
- Intellectual Property
- Life Sciences
- Materials
- Tech Scout
- Unparalleled Data Quality
- Higher Quality Content
- 60% Fewer Hallucinations
Browse by: Latest US Patents, China's latest patents, Technical Efficacy Thesaurus, Application Domain, Technology Topic, Popular Technical Reports.
© 2025 PatSnap. All rights reserved.Legal|Privacy policy|Modern Slavery Act Transparency Statement|Sitemap|About US| Contact US: help@patsnap.com