A system and method for flue gas purification and waste heat utilization
A flue gas purification and flue gas technology, applied in chemical instruments and methods, separation methods, lighting and heating equipment, etc., can solve the problem of inability to effectively solve the problem of dioxin resynthesis, the degree of waste heat utilization and the depth of purification are not ideal, etc. problems, to achieve the effect of inhibiting resynthesis, saving power consumption and reducing costs
- Summary
- Abstract
- Description
- Claims
- Application Information
AI Technical Summary
Problems solved by technology
Method used
Image
Examples
Embodiment 1
[0085] This embodiment provides a flue gas purification and waste heat utilization method, using a flue gas purification and waste heat utilization system provided in a specific embodiment to perform deep purification of flue gas and multi-effect utilization of flue gas waste heat. Described method specifically comprises the steps:
[0086] S1 The air induction device 7 draws out the flue gas produced by the fourth hole of the electric furnace 1, and the flue gas flow rate is 200,000m 3 / h, the temperature of the flue gas is 1200°C, and the flue gas discharged from the fourth hole of the electric furnace 1 includes dust, CO, NO x or a combination of one or at least two of dioxins, wherein the dust concentration is 10g / m 3 , the CO concentration is 1%, the content of dioxin is 2ng-TEQ / m 3 , NO x The content is 200ppm, and the ammonia injection device sprays ammonia into the flue gas for SNCR reaction to remove 50% of NO in the flue gas x , the injected ammonia and the NO in...
Embodiment 2
[0094] This embodiment provides a flue gas purification and waste heat utilization method, using a flue gas purification and waste heat utilization system provided in a specific embodiment to perform deep purification of flue gas and multi-effect utilization of flue gas waste heat. Described method specifically comprises the steps:
[0095] S1 The air induction device 7 draws out the flue gas produced by the fourth hole of the electric furnace 1, and the flue gas flow rate is 250000m 3 / h, the temperature of the flue gas is 1250°C, and the flue gas discharged from the fourth hole of the electric furnace 1 includes dust, CO, NO x Or one or a combination of at least two of dioxins, wherein the dust concentration is 13g / m 3 , the CO concentration is 5%, and the content of dioxin is 4ng-TEQ / m 3 , NO x The content is 700ppm, and the ammonia injection device sprays ammonia into the flue gas for SNCR reaction to remove 55% of NO in the flue gas x , the injected ammonia and the NO...
Embodiment 3
[0103] This embodiment provides a flue gas purification and waste heat utilization method, using a flue gas purification and waste heat utilization system provided in a specific embodiment to perform deep purification of flue gas and multi-effect utilization of flue gas waste heat. Described method specifically comprises the steps:
[0104] S1 The air induction device 7 draws out the flue gas produced by the fourth hole of the electric furnace 1, and the flue gas flow rate is 300,000m 3 / h, the temperature of the flue gas is 1300°C, and the flue gas discharged from the fourth hole of the electric furnace 1 includes dust, CO, NO x Or one or a combination of at least two of dioxins, wherein the dust concentration is 15g / m 3 , the CO concentration is 10%, and the content of dioxin is 6ng-TEQ / m 3 , NO x The content is 1200ppm, and the ammonia injection device sprays ammonia into the flue gas for SNCR reaction to remove 60% of NO in the flue gas x , the injected ammonia and the...
PUM
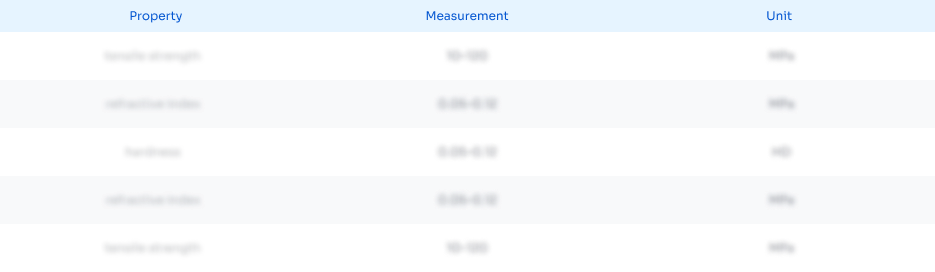
Abstract
Description
Claims
Application Information

- R&D Engineer
- R&D Manager
- IP Professional
- Industry Leading Data Capabilities
- Powerful AI technology
- Patent DNA Extraction
Browse by: Latest US Patents, China's latest patents, Technical Efficacy Thesaurus, Application Domain, Technology Topic, Popular Technical Reports.
© 2024 PatSnap. All rights reserved.Legal|Privacy policy|Modern Slavery Act Transparency Statement|Sitemap|About US| Contact US: help@patsnap.com