Ground glaze and preparation method thereof, as well as black ink-jet ceramic tile and manufacturing method thereof
A manufacturing method and technology of ceramic tiles, applied in the field of bottom glaze and its preparation, black inkjet ceramic tiles and its manufacture, can solve problems such as prone to glaze avoidance defects, improve appearance consistency, avoid glaze avoidance defects, increase The effect of infiltration depth
- Summary
- Abstract
- Description
- Claims
- Application Information
AI Technical Summary
Problems solved by technology
Method used
Image
Examples
Embodiment 1
[0061] This embodiment provides a bottom glaze, the raw material composition of the bottom glaze includes: 5 parts of kaolin, 33 parts of potassium feldspar, 28 parts of albite, 10 parts of quartz powder, 10 parts of zirconium silicate, 7 parts of talcum powder, 7 parts of 965 frit.
[0062] The chemical composition of the 965 frit includes in mass percent: SiO 2 49.97%, Al 2 o 3 16.96%, Fe 2 o 3 0.14%, TiO 2 0.05%, CaO 12.71%, MgO 1.41%, K 2 O 4.03%, Na 2 O 12.57%, ZnO 0.37%, B 2 o 3 0.18%, BaO 0.83%, loss on ignition 0.78%.
[0063] It can be understood that by controlling the amount of kaolin added, the infiltration depth and infiltration efficiency of the ink are increased when the inkjet printing decoration is performed on the bottom glaze, thereby improving the drying efficiency of the ink, and effectively avoiding the The avoidance of glaze defects after inkjet printing significantly improves the appearance consistency of black inkjet ceramic tiles.
Embodiment 2
[0065] This embodiment provides a bottom glaze, the raw material composition of the bottom glaze includes: 7 parts of kaolin, 33 parts of potassium feldspar, 33 parts of albite, 13 parts of quartz powder, 8 parts of zirconium silicate, Calcined soil 1 part, wollastonite 2 parts, zinc oxide 3 parts. It can be understood that by controlling the amount of kaolin added, the rate of infiltration of the ink is accelerated when the inkjet printing decoration is carried out on the bottom glaze, which effectively improves the drying efficiency of the ink, and then effectively The glaze avoidance defect after inkjet printing is avoided; at the same time, by replacing the talcum powder with wollastonite and zinc oxide, the melting effect of inkjet printing ink on the bottom glaze is effectively improved, and while the glaze avoidance defect is solved, Significantly improves the hair color effect of the ink.
Embodiment 3
[0067] see figure 1 , the present embodiment provides a method for preparing a bottom glaze, which includes,
[0068] Step S11, weighing the raw materials of the bottom glaze, and mixing the components to obtain the raw material mixture of the bottom glaze;
[0069] Step S12, according to the mass percentage of the obtained bottom glaze raw material mixture, respectively weigh 0.12% of CMC, 0.4% of sodium tripolyphosphate and 0.05% of preservative, and mix them with the bottom glaze raw material mixture to obtain the bottom glaze before ball milling. material;
[0070] Step S13, according to the weight ratio of the bottom glaze ball milling material: ball: water = 1:2:0.4, perform wet ball milling on the bottom glaze ball milling material, and control the glaze slurry after ball milling to pass through a 325-mesh sieve with a residue of 0.1 %-0.3%, get the bottom glaze.
[0071] Wherein, the raw material composition of the bottom glaze includes in terms of mass fraction: 5 ...
PUM
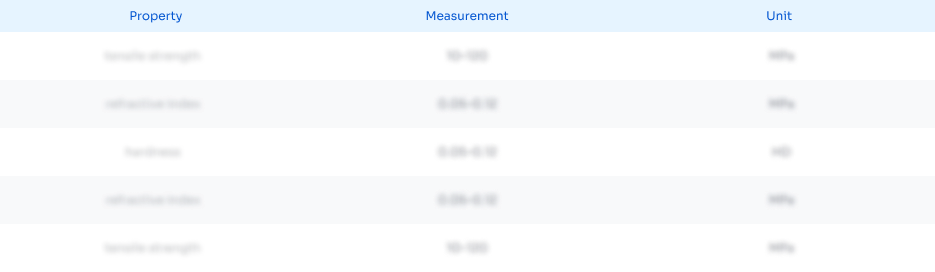
Abstract
Description
Claims
Application Information

- R&D
- Intellectual Property
- Life Sciences
- Materials
- Tech Scout
- Unparalleled Data Quality
- Higher Quality Content
- 60% Fewer Hallucinations
Browse by: Latest US Patents, China's latest patents, Technical Efficacy Thesaurus, Application Domain, Technology Topic, Popular Technical Reports.
© 2025 PatSnap. All rights reserved.Legal|Privacy policy|Modern Slavery Act Transparency Statement|Sitemap|About US| Contact US: help@patsnap.com