Method for preparing anode material of S-Ni3C/NiO composite lithium-sulfur battery
A cathode material and sulfur battery technology, applied in the field of material chemistry, can solve problems such as poor cycle stability, obvious shuttle effect, and low sulfur load
- Summary
- Abstract
- Description
- Claims
- Application Information
AI Technical Summary
Problems solved by technology
Method used
Image
Examples
Embodiment 1
[0027] The first step is to prepare Ni-BTC material:
[0028] Mix 20mL deionized water, 20mL absolute ethanol, 20mL N, N dimethylformamide according to volume ratio 1:1:1, add 0.6g nickel nitrate, 0.4g trimesic acid, 2.5g polyvinylpyrrolidone, stir 1h, ultrasound 1h. After completion, it was transferred to a polytetrafluoroethylene-lined stainless steel reactor, and kept at 180°C for 12 hours. After completion, the product was collected, washed with methanol three times, and then dried to obtain a Ni-BTC material.
[0029] The second step is to prepare Ni 3 C / NiO material:
[0030] Spread 0.8g of Ni-BTC prepared in step 1 on a porcelain boat, raise the temperature to 350°C at a rate of 1°C / min under an argon atmosphere, keep it warm for 2 hours, and heat it at a temperature of 30mL / min during the heat preservation process. Feed hydrogen gas into the tube furnace at a rate of 15 minutes, then continue to heat up to 450 ° C, and feed acetylene gas into the tube furnace at a r...
Embodiment 2
[0034] The first step is to prepare Ni-BTC material:
[0035] Mix 15mL deionized water, 15mL absolute ethanol, 15mL N, N dimethylformamide according to volume ratio 1:1:1, add 0.5g nickel nitrate, 0.3g trimesic acid, 2g polyvinylpyrrolidone, stir for 0.5 h, ultrasonic 0.5h. After the completion, it was transferred to a polytetrafluoroethylene-lined stainless steel reaction kettle, and kept at 160 degrees Celsius for 12 hours. After the reaction was completed, the product was collected, washed with methanol three times, and then dried.
[0036] The second step is to prepare Ni 3 C / NiO material:
[0037] Spread 0.5g of the Ni-BTC material prepared in step 1 on a porcelain boat, raise the temperature to 300°C at a rate of 0.5°C / min under an argon atmosphere, keep it warm for 1h, and heat it at 20mL / min during the heat preservation process. Pass hydrogen into the tube furnace at a rate of 10 min, then continue to heat up to 400 ° C, and pass acetylene gas into the tube furnace ...
Embodiment 3
[0041] The first step is to prepare Ni-BTC material:
[0042]Mix 30mL deionized water, 30mL absolute ethanol, 30mL N, N dimethylformamide according to volume ratio 1:1:3, add 1g nickel nitrate, 0.6g trimesic acid, 3g polyvinylpyrrolidone, stir for 1h, Ultrasound for 1h. After the completion, it was transferred to a polytetrafluoroethylene-lined stainless steel reaction kettle, and kept at 200 degrees Celsius for 24 hours. After the reaction was completed, the product was collected, washed with methanol three times, and then dried to obtain a Ni-BTC material.
[0043] The second step is to prepare Ni 3 C / NiO material:
[0044] Spread 1 g of Ni-BTC prepared in the first step on a porcelain boat, raise the temperature to 400°C at a rate of 1°C / min under an argon atmosphere, keep it warm for 2 hours, and heat it at a rate of 50mL / min during the heat preservation process. Feed hydrogen gas into the tube furnace at a rate of 20 min, then continue to heat up to 500 ° C, and feed a...
PUM
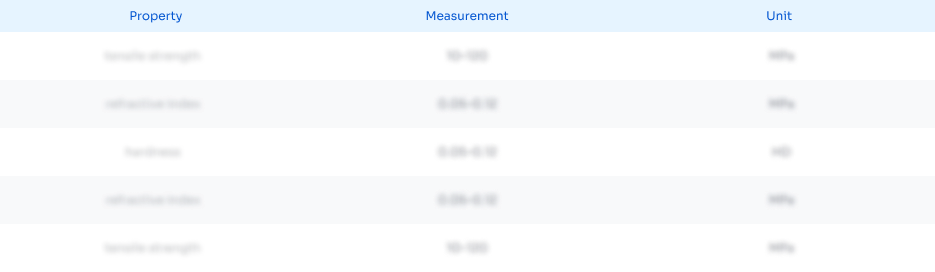
Abstract
Description
Claims
Application Information

- R&D
- Intellectual Property
- Life Sciences
- Materials
- Tech Scout
- Unparalleled Data Quality
- Higher Quality Content
- 60% Fewer Hallucinations
Browse by: Latest US Patents, China's latest patents, Technical Efficacy Thesaurus, Application Domain, Technology Topic, Popular Technical Reports.
© 2025 PatSnap. All rights reserved.Legal|Privacy policy|Modern Slavery Act Transparency Statement|Sitemap|About US| Contact US: help@patsnap.com