Test device and test method for measuring self-loosening of bolts
A test device and self-loosening technology, which is applied in the direction of measuring device, vibration test, mechanical component test, etc., can solve the problem of large difference in stiffness, inability to realize the change of degree of freedom load, and inability to meet the requirements of the anti-loosening performance test of connecting bolts, etc. problem, to achieve the effect of optimizing the anti-loosening design
- Summary
- Abstract
- Description
- Claims
- Application Information
AI Technical Summary
Problems solved by technology
Method used
Image
Examples
Embodiment Construction
[0021] In order to make the present invention more obvious and understandable, the preferred embodiments are described in detail as follows in conjunction with the accompanying drawings:
[0022] Such as figure 1 As shown, a test device for measuring the self-loosening of bolts includes an outer frame 10, a first clamping plate 1, a second clamping plate 2, a pressure sensor 3, a horizontal spring 4, a horizontal spring 5, a horizontal spring 6, a horizontal Spring 7, vertical spring 8 and vertical spring 9; The outer frame is a cube-shaped steel frame, and six faces of the outer frame form six faces of a cube; The first clamping plate 1 and the second clamping plate are provided in the center of the cube. Two clamping plates 2, the first clamping plate 1 and the second clamping plate 2 are square plate structures; the first clamping plate 1 and the second clamping plate 2 are connected by bolts 11, and the first clamping plate 1 and the second clamping plate 2 are connected b...
PUM
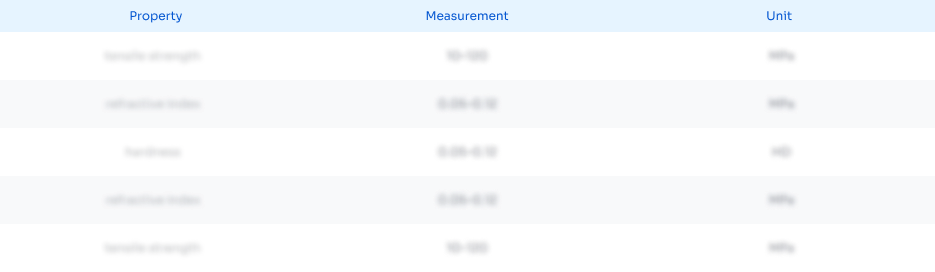
Abstract
Description
Claims
Application Information

- R&D Engineer
- R&D Manager
- IP Professional
- Industry Leading Data Capabilities
- Powerful AI technology
- Patent DNA Extraction
Browse by: Latest US Patents, China's latest patents, Technical Efficacy Thesaurus, Application Domain, Technology Topic, Popular Technical Reports.
© 2024 PatSnap. All rights reserved.Legal|Privacy policy|Modern Slavery Act Transparency Statement|Sitemap|About US| Contact US: help@patsnap.com