Spindle oil cooling system, spindle oil temperature control method and machine tool cooling machine system
A cooling system and spindle oil technology, which is applied in the manufacture of tools, maintenance and safety accessories, metal processing machinery parts, etc., can solve the problems of uncontrollable spindle oil heat exchange, high equipment costs and operating costs, and improve energy utilization. , Improve the utilization rate and avoid the effect of excessive heat exchange
- Summary
- Abstract
- Description
- Claims
- Application Information
AI Technical Summary
Problems solved by technology
Method used
Image
Examples
Embodiment 1
[0036] like Figure 1 to Figure 3 , a spindle oil cooling system, comprising a spindle oil cooling device 3, an oil inlet pipeline 5, an oil outlet pipeline 6, an oil inlet sensing probe 10, and an oil outlet sensing probe 11; the spindle oil cooling device 3 includes an evaporator 31; The oil outlet end of the evaporator 31 communicates with the oil outlet pipeline 6; it also includes an economizer 4, an inlet pipeline 7, an outlet pipeline 8, a bypass regulating valve 9 and an inlet sensor probe 12. Wherein, the economizer 4 is in heat exchange communication with the evaporator 31 and its oil inlet end is in communication with the oil inlet pipeline 5; the liquid inlet pipeline 7 is in communication with the liquid inlet end of the economizer 4 and is used for communicating Cutting fluid; the liquid outlet pipeline 8 communicates with the liquid outlet end of the economizer 4 and is used for passing the cutting fluid; the bypass regulating valve 9 is arranged between the liq...
Embodiment 2
[0093] In this specific embodiment, the spindle oil cooling system of this example is basically the same as that of the embodiment, the difference is that the economizer 4 and the bypass regulating valve 9 of the spindle oil cooling system are changed to the cutting fluid cooling device 2, which can also achieve Energy saving purpose. However, because the cutting fluid cooling device 2 is inconvenient to obtain the set oil temperature of the spindle oil cooling system, it is impossible to precisely control the spindle oil temperature by controlling the heat exchange of the economizer 4 .
PUM
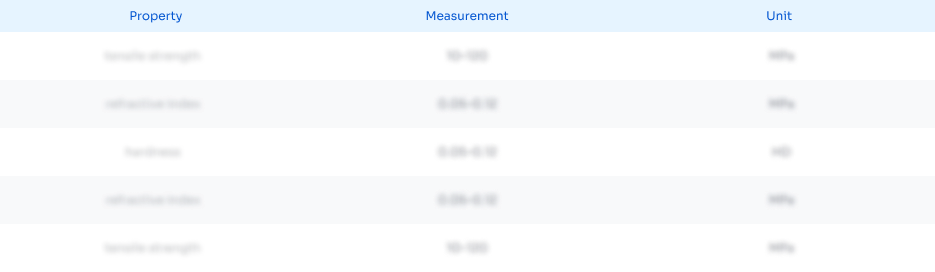
Abstract
Description
Claims
Application Information

- Generate Ideas
- Intellectual Property
- Life Sciences
- Materials
- Tech Scout
- Unparalleled Data Quality
- Higher Quality Content
- 60% Fewer Hallucinations
Browse by: Latest US Patents, China's latest patents, Technical Efficacy Thesaurus, Application Domain, Technology Topic, Popular Technical Reports.
© 2025 PatSnap. All rights reserved.Legal|Privacy policy|Modern Slavery Act Transparency Statement|Sitemap|About US| Contact US: help@patsnap.com