Parallel robot with large working space and low inertia
A work space, low inertia technology, applied in manipulators, manufacturing tools, program-controlled manipulators, etc., can solve the problems of complex kinematic model, difficult manufacturing and assembly, small driving angle of the mechanism, etc., and achieve simple kinematic and dynamic models. , Easy motion control and manufacturing, the effect of large operating angles
- Summary
- Abstract
- Description
- Claims
- Application Information
AI Technical Summary
Problems solved by technology
Method used
Image
Examples
Embodiment 1
[0019] see figure 1 , 3, 4, a parallel robot with a large working space and low inertia, including a frame 1, a moving table 2, three identical and along the center of the frame between the connecting frame 1 and the moving table 2 The axis is evenly distributed around the branch; each branch from the frame 1 to the moving console 2 is a parallelogram coupling driving assembly, the sixth rotating joint assembly R6, the driven rod L5, the seventh rotating joint assembly R7, and the universal Hinge assembly U1; the parallelogram coupling drive assembly is connected with the driven rod L5 through the sixth rotating joint assembly R6, and the axis of the sixth rotating joint R6 is perpendicular to the center line of the driven rod L5; the driven The rod L5 is connected to the universal joint assembly U1 through the seventh rotary joint assembly R7, and the axis of the seventh rotary joint assembly R7 coincides with the center line of the driven rod L5; the universal joint assembl...
Embodiment 2
[0021] see figure 2 As shown, the difference between Embodiment 2 and Embodiment 1 is that the axis of the rotary joint in the universal joint assembly U1 close to the movable console 2 is parallel to or oblique to the plane where the movable console 2 is located.
PUM
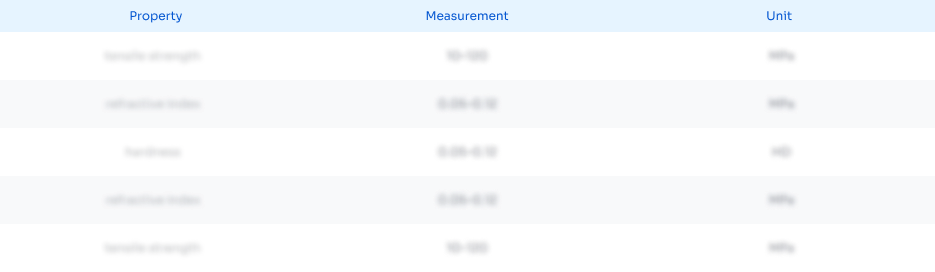
Abstract
Description
Claims
Application Information

- R&D
- Intellectual Property
- Life Sciences
- Materials
- Tech Scout
- Unparalleled Data Quality
- Higher Quality Content
- 60% Fewer Hallucinations
Browse by: Latest US Patents, China's latest patents, Technical Efficacy Thesaurus, Application Domain, Technology Topic, Popular Technical Reports.
© 2025 PatSnap. All rights reserved.Legal|Privacy policy|Modern Slavery Act Transparency Statement|Sitemap|About US| Contact US: help@patsnap.com