Internal Error Calibration Compensation System and Calibration Compensation Method of Photon Interference Imaging System
A technology of interference imaging and error calibration, applied in the field of optical interference imaging, can solve problems such as device errors and affecting imaging system performance, and achieve the effects of reducing volume, improving imaging quality, and improving reliability and stability
- Summary
- Abstract
- Description
- Claims
- Application Information
AI Technical Summary
Problems solved by technology
Method used
Image
Examples
specific Embodiment approach 1
[0034] Specific implementation mode 1. Combination figure 2Description of this embodiment, the internal error calibration and compensation system of the photon interference imaging system includes a calibration light source (thorlab 1550nm infrared laser), a phase adjustment device (general photonics electronic delay line), a PIC chip to be tested, and a light intensity detection device (short-wave infrared camera) , 1*2 fiber optic coupler, fiber optic jumper, etc. The PIC chip to be tested has two input ports and four output ports. The interior only includes a set of interferometers, which are composed of a pair of waveguides and a beam combiner. The waveguide mainly transmits light and adjusts the optical path. The beam combiner performs interference and completes the sampling of the fringes at quarter-period intervals.
[0035] One end of the optical fiber coupler is connected to the calibration light source, so that the calibration light source is divided into two outpu...
specific Embodiment approach 2
[0037] Specific embodiment two, combine image 3 Describe this implementation mode, this implementation is the calibration compensation method of the internal error calibration compensation system of the photon interference imaging system described in the specific implementation mode 1, establish a mathematical model of the PIC photonic integrated chip, calibrate the internal error of the system, and then re-image During the construction process, the calibration data is used to compensate for the error. By adopting a phase-locked dual light source calibration compensation method, and by controlling the light intensity and phase difference of the calibration light source, the high-precision error calibration compensation of the PIC chip to be tested is realized. This method adopts phase-locked dual light source calibration compensation, which is realized by the following steps:
[0038] 1. Establish a mathematical model of the input and output of the PIC chip to be tested. The...
PUM
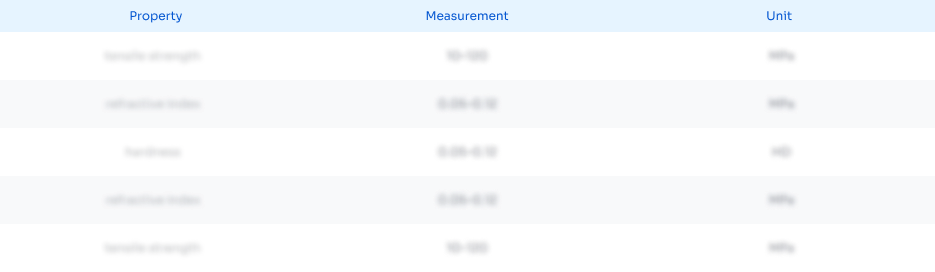
Abstract
Description
Claims
Application Information

- R&D
- Intellectual Property
- Life Sciences
- Materials
- Tech Scout
- Unparalleled Data Quality
- Higher Quality Content
- 60% Fewer Hallucinations
Browse by: Latest US Patents, China's latest patents, Technical Efficacy Thesaurus, Application Domain, Technology Topic, Popular Technical Reports.
© 2025 PatSnap. All rights reserved.Legal|Privacy policy|Modern Slavery Act Transparency Statement|Sitemap|About US| Contact US: help@patsnap.com