PET-SR antibacterial thermal insulation glass film
A PET-SR, glass film technology, used in film/sheet adhesives, non-polymer organic compound adhesives, adhesives, etc. The problems of heat insulation and heat resistance are not revealed, and the effects of excellent anti-scratch and antibacterial functions, excellent anti-riot resistance, and low requirements for production equipment are achieved.
- Summary
- Abstract
- Description
- Claims
- Application Information
AI Technical Summary
Problems solved by technology
Method used
Examples
Embodiment 1
[0030]A PET-SR antibacterial thermal insulation glass film, comprising an antibacterial anti-scratch SR layer, a modified PET base layer and an adhesive layer, the adhesive layer is adhered to the lower surface of the modified PET base layer, wherein the modified PET base layer includes The following components in terms of mass parts: PET masterbatch, 20 parts, PE resin 10 parts, nano silicon micropowder 5 parts, PCM phase change energy storage material 1 part, diglycerin 5 parts, isooctyl palmitate 5 parts, 2 parts of chitosan, 3 parts of ethylene glycol butyl ether; the adhesive layer includes the following components in terms of mass parts: 18 parts of ethyl acrylate, 5 parts of rosin resin, and 15 parts of ethylene glycol.
[0031] The upper surface of the anti-scratch layer SR is sprayed with an antibacterial material, preferably, the antibacterial material is nano-silver.
[0032] The preparation method of the modified PET base layer is as follows:
[0033] Step 1: In t...
Embodiment 2
[0038] A PET-SR antibacterial thermal insulation glass film, comprising an antibacterial anti-scratch SR layer, a modified PET base layer and an adhesive layer, the adhesive layer is adhered to the lower surface of the modified PET base layer, wherein the modified PET base layer includes The following components in terms of mass parts: 30 parts of PET masterbatch, 12 parts of PE resin, 10 parts of nano-silica powder, 1 part of PCM phase change energy storage material, 8 parts of diglycerin, 10 parts of isooctyl palmitate, shell 3 parts of polysaccharide, 5 parts of ethylene glycol butyl ether; the adhesive layer includes the following components in parts by mass: 22 parts of ethyl acrylate, 10 parts of rosin resin, and 30 parts of ethylene glycol.
[0039] The preparation method of the modified PET base layer and the coating method of the adhesive layer are the same as in Example 1.
Embodiment 3
[0041] A PET-SR antibacterial thermal insulation glass film, comprising an antibacterial anti-scratch SR layer, a modified PET base layer and an adhesive layer, the adhesive layer is adhered to the lower surface of the modified PET base layer, wherein the modified PET base layer includes The following components in parts by mass: 21 parts of PET masterbatch, 11 parts of PE resin, 6 parts of nano-silica powder, 1.5 parts of PCM phase change energy storage material, 6 parts of diglycerin, 6 parts of isooctyl palmitate, shell 2 parts of polysaccharide, 5 parts of ethylene glycol butyl ether; the adhesive layer includes the following components in terms of mass parts: 19 parts of ethyl acrylate, 6 parts of rosin resin, and 16 parts of ethylene glycol.
[0042] The preparation method of the modified PET base layer and the coating method of the adhesive layer are the same as in Example 1.
PUM
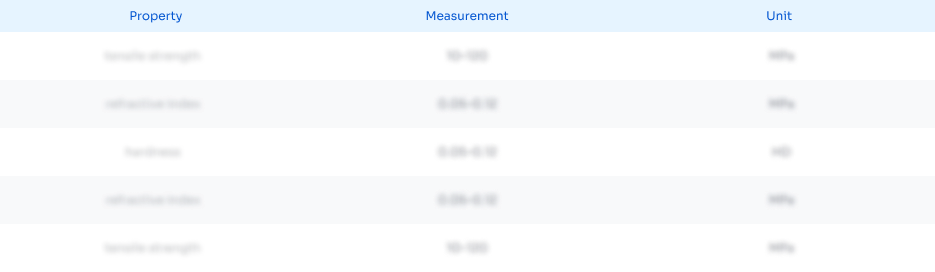
Abstract
Description
Claims
Application Information

- R&D
- Intellectual Property
- Life Sciences
- Materials
- Tech Scout
- Unparalleled Data Quality
- Higher Quality Content
- 60% Fewer Hallucinations
Browse by: Latest US Patents, China's latest patents, Technical Efficacy Thesaurus, Application Domain, Technology Topic, Popular Technical Reports.
© 2025 PatSnap. All rights reserved.Legal|Privacy policy|Modern Slavery Act Transparency Statement|Sitemap|About US| Contact US: help@patsnap.com