Machining method of butterfly-shaped composite material sandwich part
A composite material and processing method technology, which is applied in the field of composite material parts manufacturing, can solve the problems of easily damaged surfaces, long manufacturing cycle of forming molds, and high cost, and achieve the effects of completely consistent thickness, reduced manufacturing costs, and uniform pressure transmission
- Summary
- Abstract
- Description
- Claims
- Application Information
AI Technical Summary
Problems solved by technology
Method used
Image
Examples
Embodiment Construction
[0023] In this example, the butterfly-shaped composite material sandwich part is composed of the middle core layer 3, the upper panel 7 and the lower panel 8 sandwiching the upper and lower surfaces of the core layer, and the upper backing plate 1 and the lower backing plate 2 on the outer layers of the upper and lower panels. Openings with exactly the same shape and position should be processed on the backing plate, and the openings completely expose the surface of the panel below. Processing methods such as figure 1 -5 shown.
[0024] Cut the composite upper backing plate 1 and lower backing plate 2 with the same shape on the cured composite backing board wool, and process two craft pads in the wool surplus area that are completely consistent with the shape and thickness of the center opening of the backing board piece 5;
[0025] The core layer 3 and the upper and lower panels are processed into a rectangle consistent with the shape of the backing plate, and at the same t...
PUM
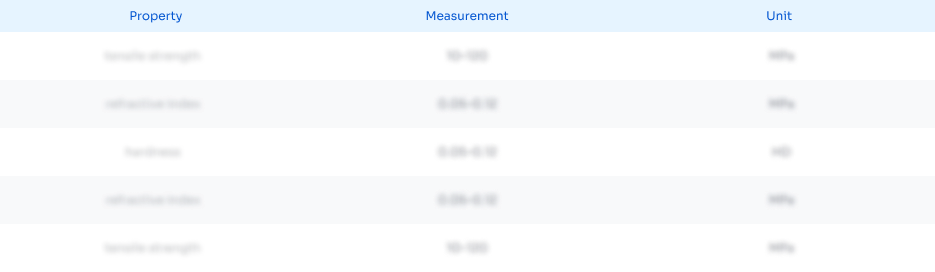
Abstract
Description
Claims
Application Information

- R&D Engineer
- R&D Manager
- IP Professional
- Industry Leading Data Capabilities
- Powerful AI technology
- Patent DNA Extraction
Browse by: Latest US Patents, China's latest patents, Technical Efficacy Thesaurus, Application Domain, Technology Topic, Popular Technical Reports.
© 2024 PatSnap. All rights reserved.Legal|Privacy policy|Modern Slavery Act Transparency Statement|Sitemap|About US| Contact US: help@patsnap.com