Carbon fiber composite mold surface forming property screening method
A composite material and surface molding technology, which is applied in the field of carbon fiber reinforced resin matrix composite material structure molding, can solve the single evaluation method of surface roughness, cannot realize comprehensive evaluation, and cannot meet the development needs of large-diameter high-precision composite antenna reflectors and other issues to achieve the effect of high reliability and shortened development cycle
- Summary
- Abstract
- Description
- Claims
- Application Information
AI Technical Summary
Problems solved by technology
Method used
Image
Examples
Embodiment Construction
[0030] Such as figure 1 Shown, a kind of carbon fiber composite mold surface formability screening method of the present invention, the steps are as follows:
[0031] (1): CNC machine tools are used to process the master mold according to the parabolic equation to produce a molding surface with a certain surface accuracy and surface roughness;
[0032] (2): The mold prepreg is used to lay the mold on the surface of the master mold in step 1. During the prepreg laying process, the prepreg is prepressed according to the prepress system of the mold prepreg resin system; After the prepreg laying is completed, according to the curing system of the mold prepreg resin system, the curing and molding of the composite mold is completed in an autoclave or an oven;
[0033] (3): After the composite material mold completes the curing and molding of step 2 on the master mold, the composite material mold is released from the master mold to ensure that there is no layered cracking damage dur...
PUM
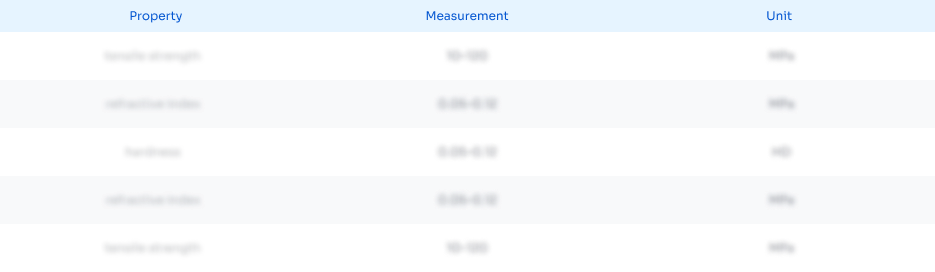
Abstract
Description
Claims
Application Information

- Generate Ideas
- Intellectual Property
- Life Sciences
- Materials
- Tech Scout
- Unparalleled Data Quality
- Higher Quality Content
- 60% Fewer Hallucinations
Browse by: Latest US Patents, China's latest patents, Technical Efficacy Thesaurus, Application Domain, Technology Topic, Popular Technical Reports.
© 2025 PatSnap. All rights reserved.Legal|Privacy policy|Modern Slavery Act Transparency Statement|Sitemap|About US| Contact US: help@patsnap.com