Automatic production line applied to machining of steel channel of forklift gantry
An automatic production line and forklift gantry technology, applied in the direction of manufacturing tools and other manufacturing equipment/tools, can solve the problems of difficult to guarantee processing quality, low production efficiency, waste of manpower and material resources, etc., to improve the efficiency of channel steel processing and welding Effect
- Summary
- Abstract
- Description
- Claims
- Application Information
AI Technical Summary
Problems solved by technology
Method used
Image
Examples
Embodiment Construction
[0034] In the description of the present invention, unless otherwise specified, the orientation or positional relationship indicated by the terms "upper", "lower", "left", "right", "front", "rear", etc. are only for describing the present invention and simplifying the description, rather than Nothing indicating or implying that the referred device or structure must have a particular orientation should not be construed as limiting the invention. In addition, the terms "first", "second", etc. are used for descriptive purposes only, and should not be construed as indicating or implying relative importance.
[0035] An automatic production line for processing channel steel of a forklift mast according to the present invention includes a first machining center, a first positioning mold, a second machining center, a second positioning mold, a channel steel turning center, a guide roller table, The roller shaft welding station and the clamping roller table, wherein the first machinin...
PUM
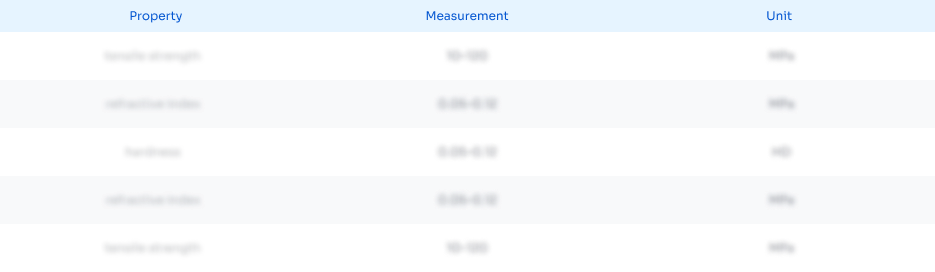
Abstract
Description
Claims
Application Information

- R&D
- Intellectual Property
- Life Sciences
- Materials
- Tech Scout
- Unparalleled Data Quality
- Higher Quality Content
- 60% Fewer Hallucinations
Browse by: Latest US Patents, China's latest patents, Technical Efficacy Thesaurus, Application Domain, Technology Topic, Popular Technical Reports.
© 2025 PatSnap. All rights reserved.Legal|Privacy policy|Modern Slavery Act Transparency Statement|Sitemap|About US| Contact US: help@patsnap.com