A Composite Additive Manufacturing Method for Conformally Cooling Molds
A conformal cooling and additive manufacturing technology, applied in the field of additive manufacturing, can solve the problems of low mold surface accuracy, poor shape regularity of the upper arm of the cavity, and uneven inner wall, etc., to improve cooling performance, large heat source radius, and thermal Enter high effect
- Summary
- Abstract
- Description
- Claims
- Application Information
AI Technical Summary
Problems solved by technology
Method used
Image
Examples
Embodiment 1
[0027] figure 1 It is a schematic diagram of the process flow of the present invention, and the process mainly includes four processes of milling semicircular grooves and grooves on the substrate, welding positioning of pipes, surfacing filling, and laser synchronous powder feeding and additive manufacturing of the surface layer.
[0028] figure 2 To process the groove and bevel pattern for the substrate of the present invention, a semi-circular arc with the same diameter as the outer diameter of the cooling pipe is machined on the substrate, and then beveled on both sides of the arc. The base material is pre-hardened P20 forged material.
[0029] Place the stainless steel tube or copper tube inside the arc groove, use the fixture to position, and then use argon arc welding to weld and fix the tube and the substrate. The stainless steel pipe used in this embodiment is a 316L stainless steel pipe with a wall thickness of 3mm.
[0030] Then, the plasma arc additive manufactu...
PUM
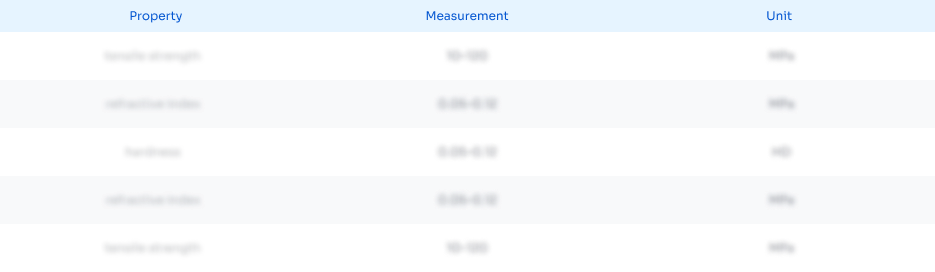
Abstract
Description
Claims
Application Information

- Generate Ideas
- Intellectual Property
- Life Sciences
- Materials
- Tech Scout
- Unparalleled Data Quality
- Higher Quality Content
- 60% Fewer Hallucinations
Browse by: Latest US Patents, China's latest patents, Technical Efficacy Thesaurus, Application Domain, Technology Topic, Popular Technical Reports.
© 2025 PatSnap. All rights reserved.Legal|Privacy policy|Modern Slavery Act Transparency Statement|Sitemap|About US| Contact US: help@patsnap.com