High-performance copper alloy strip grinding device
A copper alloy strip and grinding device technology, applied in abrasive belt grinders, grinders, metal processing equipment, etc., can solve the scrapping of grinding rollers and idlers, increase the wear, creasing and scratches of grinding rollers and idlers, etc. problems, to achieve the effect of improving grinding quality, prolonging service life and reducing grinding pressure
- Summary
- Abstract
- Description
- Claims
- Application Information
AI Technical Summary
Problems solved by technology
Method used
Image
Examples
Embodiment Construction
[0026] The present invention can be explained in detail through the following examples, and the purpose of disclosing the present invention is to protect all technical improvements within the scope of the present invention.
[0027]A high-performance copper alloy strip grinding device, including an upper belt surface grinding device and a lower belt surface grinding device; one upper belt surface grinding device and one lower belt surface grinding device are set as a set of grinding devices, and the upper belt surface grinding device The device is aligned with the center line of the lower belt surface grinding device, and is set up sequentially and separately along the moving direction of the copper alloy strip; there are three sets of high-performance copper alloy strip grinding devices, and the center line of each group of grinding devices is aligned, along the direction of copper alloy strip grinding. Strip moving direction sequence, separation and fixed setting;
[0028] T...
PUM
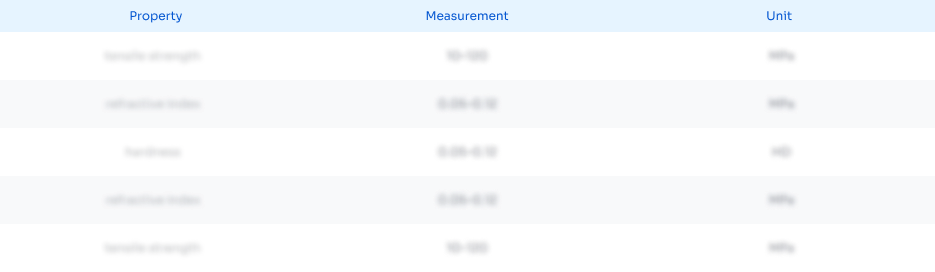
Abstract
Description
Claims
Application Information

- R&D Engineer
- R&D Manager
- IP Professional
- Industry Leading Data Capabilities
- Powerful AI technology
- Patent DNA Extraction
Browse by: Latest US Patents, China's latest patents, Technical Efficacy Thesaurus, Application Domain, Technology Topic, Popular Technical Reports.
© 2024 PatSnap. All rights reserved.Legal|Privacy policy|Modern Slavery Act Transparency Statement|Sitemap|About US| Contact US: help@patsnap.com