Square bloom continuous casting manufacturing method facilitating elimination of core defects
A manufacturing method and bloom technology, applied in the field of large-section billet production, can solve problems such as ineffective elimination of core loose shrinkage cavity defects, adverse effects on product comprehensive performance, and poor flow feeding ability of steel materials, etc., to achieve Optimize the effect of shrinkage cavity defect elimination, reduce the risk of occurrence, and the effect of high porosity elimination ability
- Summary
- Abstract
- Description
- Claims
- Application Information
AI Technical Summary
Problems solved by technology
Method used
Image
Examples
Embodiment Construction
[0036] Preferred embodiments of the present invention will be described in detail below with reference to the accompanying drawings. In order to make the following explanations easier to understand, the key equipment structures are enlarged, and the specific size ratios in the schematic diagrams are not limited to be consistent with the actual situation.
[0037] Taking the application of this continuous casting manufacturing method in the production of blooms with a cross-section of 300mm×360mm as an example, the refined molten steel enters the mold 2 through the tundish 1, and a continuous state of solid-liquid coexistence is formed as the molten steel in contact with the mold solidifies. Slab 4. The continuous casting slab 4 is stably pulled out from the bottom of the crystallizer 2 and then enters the secondary cooling zone 3. The casting speed is 0.6m / min to ensure a stable continuous casting slab production process and also to form a large core surface temperature gradie...
PUM
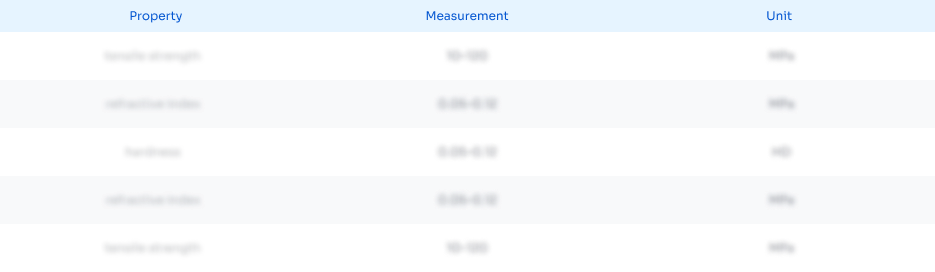
Abstract
Description
Claims
Application Information

- R&D
- Intellectual Property
- Life Sciences
- Materials
- Tech Scout
- Unparalleled Data Quality
- Higher Quality Content
- 60% Fewer Hallucinations
Browse by: Latest US Patents, China's latest patents, Technical Efficacy Thesaurus, Application Domain, Technology Topic, Popular Technical Reports.
© 2025 PatSnap. All rights reserved.Legal|Privacy policy|Modern Slavery Act Transparency Statement|Sitemap|About US| Contact US: help@patsnap.com