Curing and drying method for lead battery plates
A curing and drying technology for lead-acid batteries, applied to the electrodes of lead-acid batteries, etc., can solve problems such as temperature inconsistency, low production efficiency, and poor plate consistency, so as to prolong cycle life, improve production efficiency, and improve plate quality. The effect of temperature
- Summary
- Abstract
- Description
- Claims
- Application Information
AI Technical Summary
Problems solved by technology
Method used
Examples
Embodiment 1
[0043] The curing and drying method of the lead storage battery polar plate of the present embodiment is specifically as follows:
[0044] 1. Plate preloading stage
[0045] The temperature in the curing room is set to 45°C and the relative humidity is set to 99%. Turn on the atomization and humidification, fill the plate curing rack, push it into the curing room, and close the door of the curing room after filling.
[0046] 2. Plate preheating stage
[0047] When the curing chamber is in a sealed state, the temperature of the negative plate curing chamber is raised to 50° C. in 2 hours; the temperature of the positive plate is raised to 60° C. in 3 hours. Relying on steam heating, there is no need to turn on the circulation fan, no need to supplement oxygen, and no need to spray humidification.
[0048] 3. Recrystallization transformation stage
[0049] With the curing chamber in a sealed state, the negative plate curing chamber was kept at 50° C. for 6 hours; the positive...
Embodiment 2
[0058] 1. Plate preloading stage
[0059] The temperature in the curing room is set to 45°C and the relative humidity is set to 99%. Turn on the atomization and humidification, fill the plate curing rack, push it into the curing room, and close the door of the curing room after filling.
[0060] 2. Plate preheating stage
[0061] When the curing chamber is in a sealed state, the temperature of the negative plate curing chamber is raised to 55° C. in 3 hours; the temperature of the positive plate is raised to 75° C. in 4 hours. Relying on steam heating, there is no need to turn on the circulation fan, no need to supplement oxygen, and no need to spray humidification.
[0062] 3. Recrystallization transformation stage
[0063] With the curing chamber in a sealed state, the negative plate curing chamber was kept at 55° C. for 8 hours; the positive plate was kept at 75° C. for 8 hours. Use steam heating, still turn off the circulation fan, spray humidification.
[0064] 4. The...
PUM
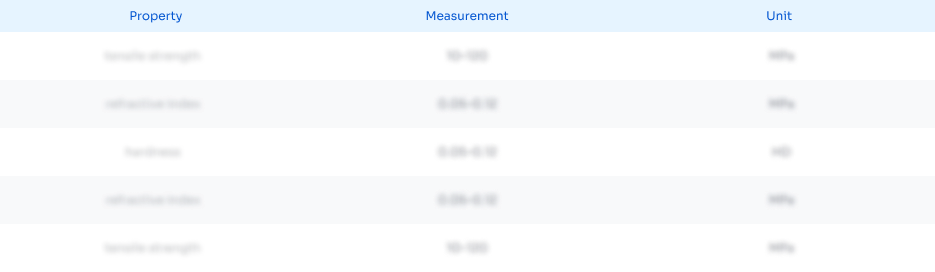
Abstract
Description
Claims
Application Information

- R&D
- Intellectual Property
- Life Sciences
- Materials
- Tech Scout
- Unparalleled Data Quality
- Higher Quality Content
- 60% Fewer Hallucinations
Browse by: Latest US Patents, China's latest patents, Technical Efficacy Thesaurus, Application Domain, Technology Topic, Popular Technical Reports.
© 2025 PatSnap. All rights reserved.Legal|Privacy policy|Modern Slavery Act Transparency Statement|Sitemap|About US| Contact US: help@patsnap.com