Clamping force control system for electronic mechanical brake of commercial vehicle and control method thereof
An electronic mechanical braking and control system technology, applied in the direction of brakes, etc., can solve the problems of only focusing on the response and following performance of the clamping force, without considering the driver's operating behavior, and poor response performance of the clamping force. reliability and reusability, shortening control time, and improving braking performance
- Summary
- Abstract
- Description
- Claims
- Application Information
AI Technical Summary
Problems solved by technology
Method used
Image
Examples
specific Embodiment approach
[0035] In order to clearly and completely describe the technical solution of the present invention and its specific working process, in conjunction with the accompanying drawings, the specific implementation of the present invention is as follows:
[0036] Such as figure 1 As shown, the present invention provides a commercial vehicle electromechanical brake clamping force control system, the control system is composed of a signal acquisition module, an upper control module, a lower control module and an actuator control module.
[0037] The actuator controlled by the actuator control module includes a three-phase brushless DC motor, a screw and nut mechanism, a push rod mechanism and an air pressure disc brake caliper, wherein the three-phase brushless DC motor is used as the power device of the brake; the screw and nut mechanism As the motion conversion device of the brake, the motion conversion device refers to a device that converts the rotary motion output by the power pla...
PUM
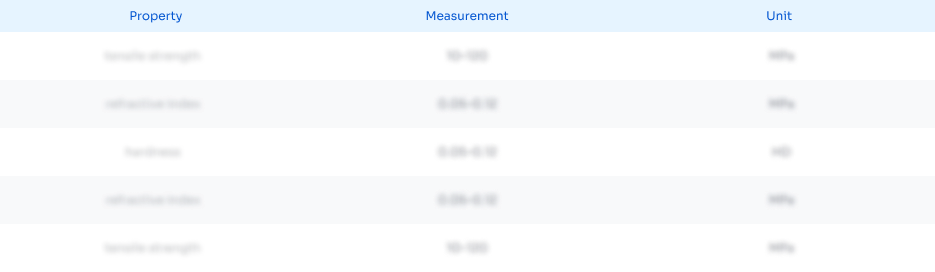
Abstract
Description
Claims
Application Information

- R&D Engineer
- R&D Manager
- IP Professional
- Industry Leading Data Capabilities
- Powerful AI technology
- Patent DNA Extraction
Browse by: Latest US Patents, China's latest patents, Technical Efficacy Thesaurus, Application Domain, Technology Topic, Popular Technical Reports.
© 2024 PatSnap. All rights reserved.Legal|Privacy policy|Modern Slavery Act Transparency Statement|Sitemap|About US| Contact US: help@patsnap.com