Nitriding device with adjustable atmosphere area and its continuous gas nitriding process
A gas nitriding, adjustable technology, applied in metal material coating process, solid diffusion coating, coating, etc., can solve problems such as under nitriding or over nitriding
- Summary
- Abstract
- Description
- Claims
- Application Information
AI Technical Summary
Problems solved by technology
Method used
Image
Examples
Embodiment 1
[0044] Such as Figure 1~2 The shown nitriding device with adjustable atmosphere area includes a nitriding chamber 1 (a heating unit is conventionally arranged in the nitriding chamber 1), a conveyor belt 2 is arranged in the nitriding chamber 1, and a conveyor belt 2 is arranged in the nitriding chamber 1. Nitriding gas delivery pipelines 3 are arranged symmetrically above both sides of the belt 2, and the nitriding gas delivery pipelines 3 are placed on the slide rail 9 laid on the side wall of the nitriding chamber 1, and slide back and forth along the slide rail 9; One end of two nitriding gas delivery pipelines 3 protrudes from the inlet end of the nitriding chamber 1 and communicates with a three-way pipe 4. The other end of the three-way pipe 4 communicates with a nitrogen delivery pipeline 5 and an ammonia delivery pipeline 6, and the nitrogen delivery Both the pipeline 5 and the ammonia delivery pipeline 6 are provided with a control valve 10 to control the ratio of n...
Embodiment 2
[0059] The length of the nitriding gas delivery pipeline Ll=4100mm, the length of the nozzle area Ln=600mm, adjust the internal temperature of the nitriding chamber according to different nitriding process requirements, and then connect the sample with the thermocouple and pass the plate at the set speed Vs, so that The temperature curve holding platform time tn meets the process requirements. If the temperature and time do not meet the requirements, repeatedly adjust the furnace temperature and measure again until the process requirements are met. According to the measured curve, determine the time ts ( image 3 ), calculate the length Lr of the nitriding tube reserved outside the furnace, manually slide the nitriding gas input pipe, so that the length of the reserved part outside the furnace is equal to Lr, and feed N 2 +NH 3 , the flow rate is fixed, where NH 3 The ratio is greater than 60%, and the nitriding results are shown in Table 1. As a comparison, the comparativ...
Embodiment 3
[0068] Using Examples 1-3 in Example 1 above, the ammonia ratio in the nitriding mixture was adjusted, and the results are shown in Table 2 below. It can be seen from the table that when the ammonia gas ratio exceeds 50%, the nitriding efficiency is significantly improved. When the ammonia gas flow rate is 80%, the nitriding amount is the highest and the efficiency is the best. Table 2 Nitriding results of different ammonia gas ratios
[0069]
PUM
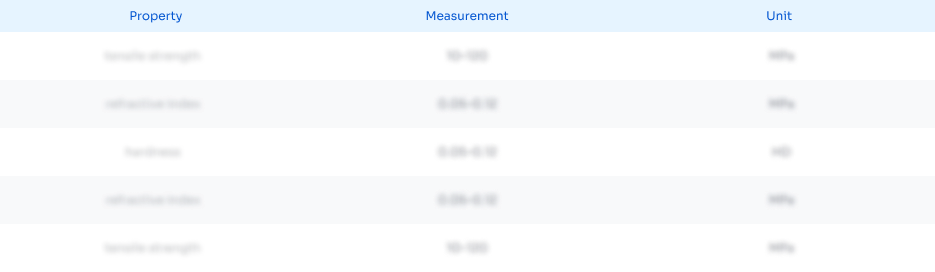
Abstract
Description
Claims
Application Information

- R&D Engineer
- R&D Manager
- IP Professional
- Industry Leading Data Capabilities
- Powerful AI technology
- Patent DNA Extraction
Browse by: Latest US Patents, China's latest patents, Technical Efficacy Thesaurus, Application Domain, Technology Topic, Popular Technical Reports.
© 2024 PatSnap. All rights reserved.Legal|Privacy policy|Modern Slavery Act Transparency Statement|Sitemap|About US| Contact US: help@patsnap.com