Composite forming method of component with large-angle thin-wall twisted narrow-depth cavity feature
A compound forming and large-angle technology, applied in the field of mechanical engineering, can solve problems such as poor structural rigidity, long manufacturing cycle, and low material utilization rate, and achieve the effects of reducing processing difficulty and cost, good cutting surface quality, and improving convenience
- Summary
- Abstract
- Description
- Claims
- Application Information
AI Technical Summary
Problems solved by technology
Method used
Image
Examples
Embodiment Construction
[0024] The present invention will be described in detail below in conjunction with the accompanying drawings and specific embodiments. This embodiment is carried out on the premise of the technical solution of the present invention, and detailed implementation and specific operation process are given, but the protection scope of the present invention is not limited to the following embodiments.
[0025] This embodiment provides a compound forming method for a component with large-angle thin-wall twist and narrow deep cavity, which specifically includes model reconstruction, mold manufacturing and processing. Such as figure 1 with figure 2 As shown, the component to be processed in this embodiment is a light-weight high-strength alloy thin-walled part, including an integrally formed bottom 1 and two side-wing thin-walls 2, and the three sides of the two side-wing thin-walls 2 and the bottom 1 jointly form a twisted narrow deep Cavity 3, when the component and the blade are c...
PUM
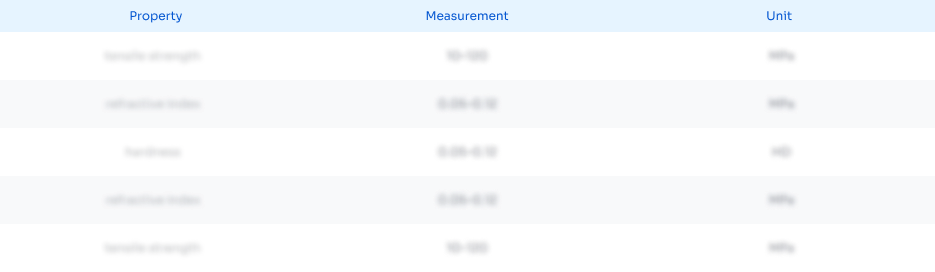
Abstract
Description
Claims
Application Information

- R&D Engineer
- R&D Manager
- IP Professional
- Industry Leading Data Capabilities
- Powerful AI technology
- Patent DNA Extraction
Browse by: Latest US Patents, China's latest patents, Technical Efficacy Thesaurus, Application Domain, Technology Topic, Popular Technical Reports.
© 2024 PatSnap. All rights reserved.Legal|Privacy policy|Modern Slavery Act Transparency Statement|Sitemap|About US| Contact US: help@patsnap.com