Steel core aluminum stranded wire aluminum embedded tensile wire clamp structure
A technology of steel-cored aluminum stranded wire and tension clamp, applied in the direction of adjusting/maintaining mechanical tension, etc., can solve the problems of biting the steel wire of the steel stranded wire, insufficient crimping pressure, gaps in the aluminum stranded wire, etc., so as to reduce the labor intensity , The effect of reducing engineering costs and high crimping quality
- Summary
- Abstract
- Description
- Claims
- Application Information
AI Technical Summary
Problems solved by technology
Method used
Image
Examples
Embodiment 1
[0022] Embodiment 1: as Figure 1-5 As shown, a steel-cored aluminum stranded wire embedded aluminum tension clamp structure, including casing clamp 1, steel anchor crimping tube 2, steel core embedded aluminum tube 3, inner embedded layer aluminum tube 4, outer embedded layer aluminum tube 5 , wire shaping ring 6 and clamp anchor ring 7, steel core embedded aluminum tube 3 is sleeved on steel strand 8 at the crimping end of steel cored aluminum stranded wire, and steel anchor crimping tube 2 is sleeved outside steel core embedded aluminum tube 3 , crimping the steel anchor crimping tube 2 so that the steel core embedded aluminum tube 3 closely fits the steel strand 3 to form a steel strand crimping joint; the inner layer aluminum tube 4 is placed on the steel strand of the steel core aluminum strand at the crimping end Between the wire 7 and the inner aluminum stranded wire layer 9, the steel cored aluminum stranded wire at the crimping end is connected with the outer embedde...
Embodiment 2
[0026] Embodiment 2: A full-tension aluminum-embedded crimping method for aluminum-steel-cored stranded wires, the steps of which are as follows:
[0027] 1) Cut off the aluminum stranded wire at the crimping end of the steel-cored aluminum stranded wire to expose the steel core, the length of the cut-off section = the length of the steel anchor crimping tube + 20mm;
[0028] 2) Pull the crimping end of the steel-cored aluminum stranded wire with the set length of the aluminum stranded wire to 10 meters, insert the aluminum sleeve clamp 1 from the end of the steel-cored aluminum stranded wire, and move the aluminum sleeve clamp 1 to the Does not affect the position of the next process;
[0029] 3) Insert the steel-cored aluminum stranded wire into the outer embedded aluminum tube 5, and press the large inner diameter end of the outer embedded aluminum tube 5 towards the joint, and move the outer embedded aluminum tube to a position that does not affect the next process;
[00...
PUM
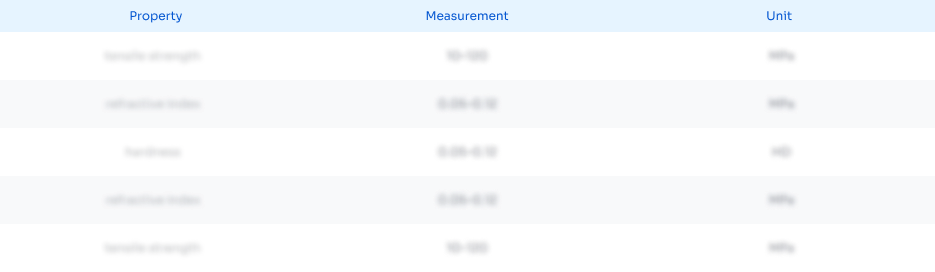
Abstract
Description
Claims
Application Information

- R&D
- Intellectual Property
- Life Sciences
- Materials
- Tech Scout
- Unparalleled Data Quality
- Higher Quality Content
- 60% Fewer Hallucinations
Browse by: Latest US Patents, China's latest patents, Technical Efficacy Thesaurus, Application Domain, Technology Topic, Popular Technical Reports.
© 2025 PatSnap. All rights reserved.Legal|Privacy policy|Modern Slavery Act Transparency Statement|Sitemap|About US| Contact US: help@patsnap.com