Surface treatment method of foaming material
A foaming material and surface treatment technology, applied in the direction of coating, etc., can solve the problems of poor hydrophilicity, insignificant effect, difficult to surpass the surface hydrophilicity of foaming materials, etc., to achieve improved hydrophilicity and good hydrophilicity Effect
- Summary
- Abstract
- Description
- Claims
- Application Information
AI Technical Summary
Problems solved by technology
Method used
Image
Examples
Embodiment
[0030] A surface treatment method for foamed materials, such as figure 1 shown, including the following steps:
[0031] S1a, cutting into pieces: cutting the foamed material to form a block material for cultivating microorganisms;
[0032] S2. Pretreatment: remove impurities on the foam material, wash the foam material with distilled water and dry it;
[0033] S3. Feeding: place the foaming material in a closed processing bin;
[0034] S4. Remove gas impurities: use a vacuum pump to extract the air in the processing chamber to form a vacuum environment;
[0035] S5. Plasma treatment: set an electrode on both sides of the foaming material, inject argon and oxygen into the treatment chamber, and pass an alternating current with a working frequency of 10Mhz to the two electrodes, and the power of the alternating current is 4500W , the argon and oxygen gain energy in the electric field generated by the two electrodes and form a plasma, the plasma moves with the change of the el...
Embodiment 2
[0046] A surface treatment method for foamed materials, such as figure 2 Shown, its difference with embodiment 1 is: comprise the following steps:
[0047] S1b, slicing: cutting the foam material to form a sheet material for making clothes.
[0048] S2. Pretreatment: remove impurities on the foam material, wash the foam material with distilled water and dry it;
[0049]S3. Feeding: place the foaming material in a closed processing bin;
[0050] S4. Remove gas impurities: use a vacuum pump to extract the air in the processing chamber to form a vacuum environment;
[0051] S5. Plasma treatment: set an electrode on both sides of the foaming material, inject argon and oxygen into the treatment chamber, and pass an alternating current with a working frequency of 10Mhz to the two electrodes, and the power of the alternating current is 4500W , the argon and oxygen gain energy in the electric field generated by the two electrodes and form a plasma, the plasma moves with the change...
PUM
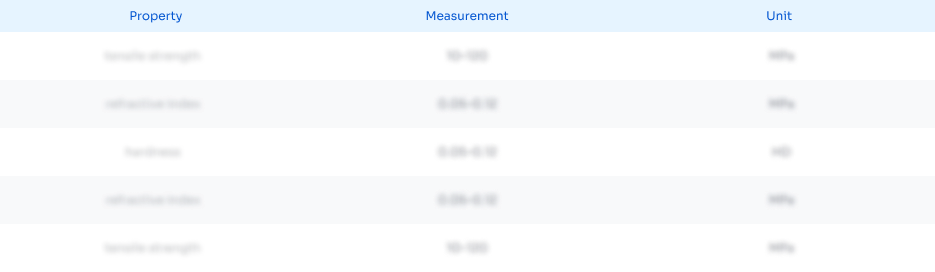
Abstract
Description
Claims
Application Information

- R&D
- Intellectual Property
- Life Sciences
- Materials
- Tech Scout
- Unparalleled Data Quality
- Higher Quality Content
- 60% Fewer Hallucinations
Browse by: Latest US Patents, China's latest patents, Technical Efficacy Thesaurus, Application Domain, Technology Topic, Popular Technical Reports.
© 2025 PatSnap. All rights reserved.Legal|Privacy policy|Modern Slavery Act Transparency Statement|Sitemap|About US| Contact US: help@patsnap.com