Magnetic powder surface gradient coating structure and coating method and soft magnetic composite
A coating structure, surface gradient technology, applied in the direction of inorganic material magnetism, metal material coating process, transportation and packaging, etc., can solve the problems of low resistivity, mismatched thermal expansion coefficient, etc. Controlled, thickness and particle size controllable effects
- Summary
- Abstract
- Description
- Claims
- Application Information
AI Technical Summary
Problems solved by technology
Method used
Image
Examples
Embodiment 1
[0050] Gradient structure SiO on the surface of Fe powder 2 -(MnZn)Fe 2 o 4 Preparation of cladding layer cladding and soft magnetic composite materials:
[0051] Take 30g of ferromagnetic powder and wash it twice with alcohol. Mix the cleaned iron powder with a small amount of deionized water and absolute ethanol, add KH550, TEOS, and MnCl to the mixture 2 4H 2 O, ZnCl 2 and FeCl 3 ·6H 2 O, the added Mn 2 + :Zn 2+ :Fe 3+ The molar ratio is 1:1:4. Dilute to 200 mL with absolute ethanol and deionized water, and the total volume ratio of absolute ethanol and deionized water added is 95%:5%. In the reaction system, the mass percent of ferromagnetic powder, surface modifier, silicon source precursor, and soluble metal salt is: 1:0.02:0.2:0.05. Install a reflux condenser, heat and reflux in a water bath, adjust the reaction temperature to 50°C, cool with running water, add an appropriate amount of ammonia NH 4 OH, adjust the pH value of the solution to about 10.5, and...
Embodiment 2
[0054] Gradient structure coating on the surface of Fe powder and Fe / SiO 2 -ZrO 2 Preparation of soft magnetic composite materials:
[0055] Take 30g of iron powder and wash it twice with alcohol. Mix the cleaned ferromagnetic powder with a small amount of deionized water and absolute ethanol, and add KH560, TEOS, zirconium isopropoxide (C 12 h 28 o 4 Zr). Dilute to 200mL with absolute ethanol and deionized water, and the total volume ratio of absolute ethanol and deionized water added is 90%:10%. In the reaction system, iron powder, KH560, TEOS, C 12 h 28 o 4 The mass percentage of Zr is: 1:0.02:0.2:0.05. Install a reflux condenser, heat and reflux in a water bath, adjust the reaction temperature to 50°C, cool with running water, add an appropriate amount of ammonia NH 4 OH, adjust the pH value of the solution to about 10, and mechanically stir for 0.5h. Continue to add an appropriate amount of citric acid H 3 C 6 h 5 o 7 , adjust the pH value of the solution t...
Embodiment 3
[0058] Gradient structure coating on the surface of FeSiCr magnetic powder and FeSiCr / SiO 2 -Al 2 o 3 Preparation of soft magnetic composite materials:
[0059] Take 30g of FeSiCr powder and wash it twice with alcohol. Mix the cleaned powder with a small amount of deionized water and absolute ethanol, and add KH570, TEOS, zirconium isopropoxide (C 12 h 28 o 4 Zr). Dilute to 200 mL with absolute ethanol and deionized water, and the total volume ratio of absolute ethanol and deionized water added is 95%:5%. In the reaction system, iron powder, KH560, TEOS, C 12 h 28 o 4 The mass percentage of Zr is: 1:0.04:0.5:0.005. Install a reflux condenser, heat and reflux in a water bath, adjust the reaction temperature to 50°C, cool with running water, add an appropriate amount of ammonia NH 4 OH, adjust the pH value of the solution to about 11, and mechanically stir for 0.5h. Continue to add an appropriate amount of citric acid H 3 C 6 h 5 o 7 , adjust the pH value of the ...
PUM
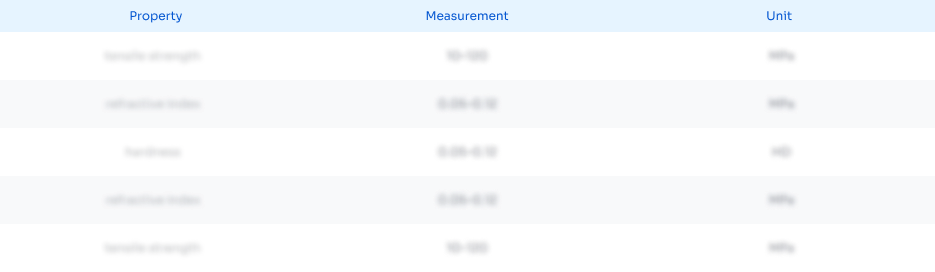
Abstract
Description
Claims
Application Information

- R&D
- Intellectual Property
- Life Sciences
- Materials
- Tech Scout
- Unparalleled Data Quality
- Higher Quality Content
- 60% Fewer Hallucinations
Browse by: Latest US Patents, China's latest patents, Technical Efficacy Thesaurus, Application Domain, Technology Topic, Popular Technical Reports.
© 2025 PatSnap. All rights reserved.Legal|Privacy policy|Modern Slavery Act Transparency Statement|Sitemap|About US| Contact US: help@patsnap.com