Preparation method for high-performance heat conductive copper powder
A high-performance, copper powder technology, applied in the field of metal powder, can solve the problems of high production cost, low powder yield, difficult control of powder porosity, etc., achieve small particle size range, increase viscosity, and improve comprehensive utilization rate Effect
- Summary
- Abstract
- Description
- Claims
- Application Information
AI Technical Summary
Problems solved by technology
Method used
Examples
preparation example Construction
[0016] The invention discloses a method for preparing high-performance thermally conductive copper powder. The specific preparation steps are as follows:
[0017] (1) The copper ingot is melted, put the copper ingot into the melting furnace, the melting temperature is controlled at a temperature of 1150°C-1250°C, and the copper ingot is melted under electromagnetic stirring;
[0018] (2) Use an air compressor to oxidize the melted copper liquid with air, and the oxidation time is 26-30 minutes, which can increase the viscosity of the copper liquid;
[0019] (3) Use the atomization method to put the copper liquid under the high pressure condition above 20Mpa, and spray the copper powder from the annular nozzle;
[0020] (4) After the atomized copper powder is dried, the dried copper powder is strictly classified. The particle size range of the copper powder is 60 mesh-80 mesh, 80 mesh-100 mesh, 100 mesh-150 mesh, 150 mesh -200 mesh, 200 mesh-300 mesh, 250-300 mesh;
[0021] (...
Embodiment 1
[0026] The invention discloses a method for preparing high-performance thermally conductive copper powder. The specific preparation steps are as follows:
[0027] (1) The copper ingot is melted, put the copper ingot into the melting furnace, the melting temperature is controlled at 1150°C, and the copper ingot is melted under electromagnetic stirring;
[0028] (2) Use an air compressor to oxidize the melted copper liquid with air, and the oxidation time is 26 minutes, which can increase the viscosity of the copper liquid;
[0029] (3) Use the atomization method to put the copper liquid under the high pressure condition above 20Mpa, and spray the copper powder from the annular nozzle;
[0030] (4) After the atomized copper powder is dried, the dried copper powder is strictly classified. The particle size range of the copper powder is 60 mesh-80 mesh, 80 mesh-100 mesh, 100 mesh-150 mesh, 150 mesh -200 mesh, 200 mesh-300 mesh, 250-300 mesh;
[0031] (5) The atomized copper powd...
Embodiment 2
[0036] The invention discloses a method for preparing high-performance thermally conductive copper powder. The specific preparation steps are as follows:
[0037] (1) The copper ingot is melted, put the copper ingot into the melting furnace, the melting temperature is controlled at 1200°C, and the copper ingot is melted under electromagnetic stirring;
[0038] (2) Use an air compressor to oxidize the melted copper liquid with air, and the oxidation time is 28 minutes, which can increase the viscosity of the copper liquid;
[0039] (3) Use the atomization method to put the copper liquid under the high pressure condition above 20Mpa, and spray the copper powder from the annular nozzle;
[0040] (4) After the atomized copper powder is dried, the dried copper powder is strictly classified. The particle size range of the copper powder is 60 mesh-80 mesh, 80 mesh-100 mesh, 100 mesh-150 mesh, 150 mesh -200 mesh, 200 mesh-300 mesh, 250-300 mesh;
[0041] (5) The atomized copper powd...
PUM
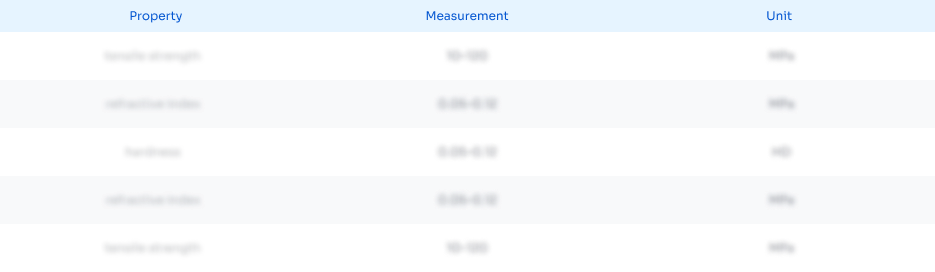
Abstract
Description
Claims
Application Information

- R&D Engineer
- R&D Manager
- IP Professional
- Industry Leading Data Capabilities
- Powerful AI technology
- Patent DNA Extraction
Browse by: Latest US Patents, China's latest patents, Technical Efficacy Thesaurus, Application Domain, Technology Topic, Popular Technical Reports.
© 2024 PatSnap. All rights reserved.Legal|Privacy policy|Modern Slavery Act Transparency Statement|Sitemap|About US| Contact US: help@patsnap.com