Cutting method and machine for PVC pinch plates
A technology of cutting machine and gusset, applied in the field of cutting machine, can solve the problems affecting the regularity of the end edge of the gusset, the collapse and deformation of the edge of the cut, and restricting the production capacity of the production line, so as to shorten the cutting time, reduce the depth of the cut, and improve the service life. Effect
- Summary
- Abstract
- Description
- Claims
- Application Information
AI Technical Summary
Problems solved by technology
Method used
Image
Examples
Embodiment Construction
[0023] A method for cutting off a PVC gusset, including a clamping step, a cutting step, a breaking step, and a resetting step,
[0024] The clamping step: fix the cutting tool holder and the gusset plate with a clamp, so that the cutting knife moves synchronously with the gusset plate in the extrusion direction of the gusset plate;
[0025] The cutting step: the cutting knife is moved horizontally on the cutting tool holder while moving synchronously with the gusset in the extrusion direction, and the moving gusset is cut laterally from the gusset plate and the lower surface, and the gusset plate The upper and lower surfaces form the corresponding upper and lower transverse incisions, and the upper and lower transverse incisions do not pass through. The upper and lower transverse incisions are rolled by a disc-shaped cutter, and the upper and lower surfaces of the gusset plate The cutting knife moves in the opposite direction, and the depth of the upper transverse incision and the...
PUM
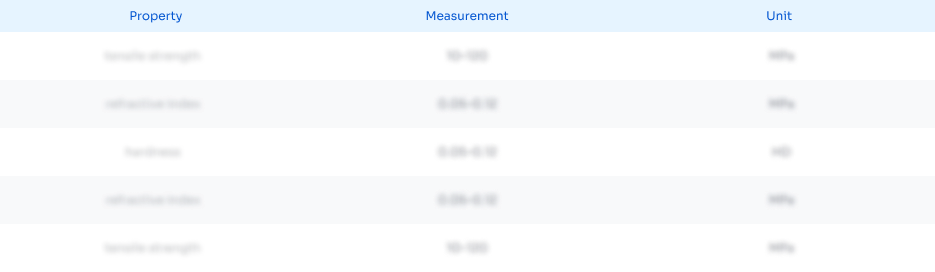
Abstract
Description
Claims
Application Information

- R&D
- Intellectual Property
- Life Sciences
- Materials
- Tech Scout
- Unparalleled Data Quality
- Higher Quality Content
- 60% Fewer Hallucinations
Browse by: Latest US Patents, China's latest patents, Technical Efficacy Thesaurus, Application Domain, Technology Topic, Popular Technical Reports.
© 2025 PatSnap. All rights reserved.Legal|Privacy policy|Modern Slavery Act Transparency Statement|Sitemap|About US| Contact US: help@patsnap.com