Preparation method of flame-retardant ABS alloy
A technology of ABS resin and alloy, which is applied in the field of composite materials, can solve problems such as complex production process, low flame retardancy, and impact on application, and achieve the effects of simple preparation process, reduced smoke generation, and high use value
- Summary
- Abstract
- Description
- Claims
- Application Information
AI Technical Summary
Problems solved by technology
Method used
Examples
Embodiment Construction
[0016] The technical scheme of the present invention will be further described below in conjunction with specific examples:
[0017] A kind of preparation method of flame-retardant ABS alloy is characterized in that, comprises the following steps:
[0018] (1) Add ABS resin, nano-calcium carbonate, flame retardant, zinc stearate, and silicone oil into the high-mixer at a mass ratio of 80:6:5:1:0.4 and mix;
[0019] (2) Put the above-mentioned uniformly mixed raw materials into a twin-screw granulator, and extrude and granulate under vacuum; the barrel temperature of the twin-screw granulator is controlled between 230-260°C, and the vacuum degree is - 0.08~-0.12MPa, the speed is 45-55Hz.
[0020] (3) Air-cool the extruded material, dry it, and cut it into pellets. The drying temperature of the material is 80-100°C, and the time is 15-30 minutes. That is, the flame-retardant ABS alloy of the present invention is obtained.
[0021] The preparation method of flame retardant:
...
PUM
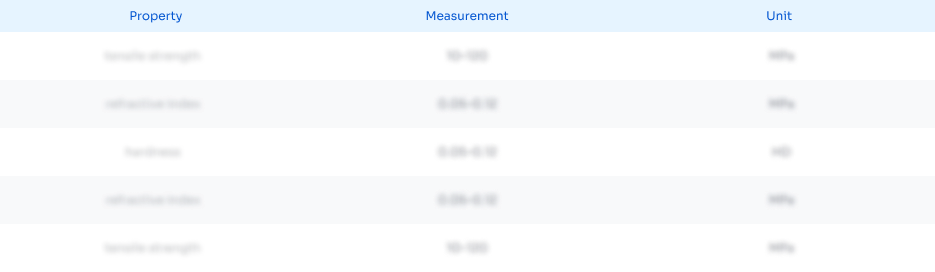
Abstract
Description
Claims
Application Information

- R&D
- Intellectual Property
- Life Sciences
- Materials
- Tech Scout
- Unparalleled Data Quality
- Higher Quality Content
- 60% Fewer Hallucinations
Browse by: Latest US Patents, China's latest patents, Technical Efficacy Thesaurus, Application Domain, Technology Topic, Popular Technical Reports.
© 2025 PatSnap. All rights reserved.Legal|Privacy policy|Modern Slavery Act Transparency Statement|Sitemap|About US| Contact US: help@patsnap.com