Production process of pre-dispersed pigment dye color chips
A production process and pre-dispersion technology, applied in ink, household utensils, applications, etc., to achieve good dispersion, high vividness, and good transparency
- Summary
- Abstract
- Description
- Claims
- Application Information
AI Technical Summary
Problems solved by technology
Method used
Examples
Embodiment 1
[0018] First, the three elements of resin, pigment and additive are stirred and mixed by a mixer, the percentage of resin is 10-85%, the percentage of pigment is 15-90%, and the percentage of additive pump is 0.1-10% ; Then the uniformly mixed material is crushed by a pulverizer; then the pigment is fully dispersed under shear through a two-roller machine, and the two-roller machine mixes and plasticizes the material through two rotating rollers with a certain speed difference. The two rollers rotate in opposite directions so that the material is strongly squeezed and sheared in the gap between the rollers, so as to achieve uniform dispersion and mixing of the pigment.
Embodiment 2
[0020] In embodiment one, add following operation:
[0021] The resin in the step (1) includes cellulose, ammonium polyacid and vinyl acetate resin, and the pigment includes inorganic pigment and organic pigment.
[0022] First, the three elements of resin, pigment and additive are stirred and mixed by a mixer, the percentage of resin is 10-85%, the percentage of pigment is 15-90%, and the percentage of additive pump is 0.1-10% , wherein the resin includes cellulose, ammonium polyacid and vinyl chloride resin, and the pigment includes inorganic pigment and organic pigment; then the uniformly mixed material is crushed by a pulverizer; then the pigment is fully dispersed under shear by a two-roller machine, The two-roll machine mixes and plasticizes the materials through two rotating rollers with a certain speed difference. The two rollers rotate in opposite directions to make the materials be strongly squeezed and sheared in the gap between the rollers, so as to achieve uniform...
Embodiment 3
[0024] In embodiment two, add following operation:
[0025] Auxiliaries in step (1) include drier, toughener, emulsifier, thickener, pigment dispersant, defoamer, leveling agent, anti-skinning agent, matting agent, light stabilizer, antifungal agent and antistatic agents.
[0026] First, the three elements of resin, pigment and additive are stirred and mixed by a mixer, the percentage of resin is 10-85%, the percentage of pigment is 15-90%, and the percentage of additive pump is 0.1-10% , wherein resins include cellulose, polyammonium and vinyl acetate resins, pigments include inorganic pigments and organic pigments, wherein auxiliary agents include driers, tougheners, emulsifiers, thickeners, pigment dispersants, defoamers, Leveling agent, anti-skinning agent, matting agent, light stabilizer, anti-fungal agent and antistatic agent; then the uniformly mixed material is crushed by a pulverizer; then the pigment is fully dispersed under shear by a two-roller machine The two-ro...
PUM
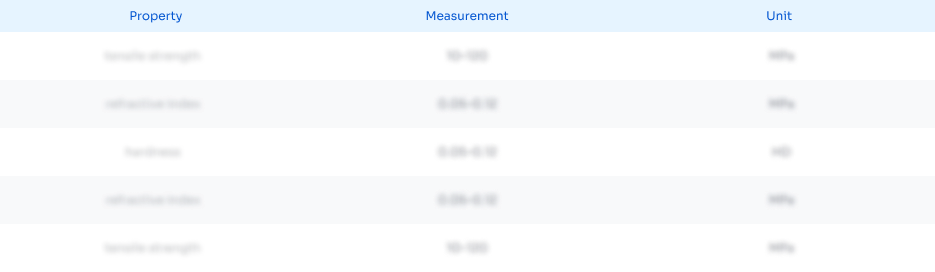
Abstract
Description
Claims
Application Information

- R&D Engineer
- R&D Manager
- IP Professional
- Industry Leading Data Capabilities
- Powerful AI technology
- Patent DNA Extraction
Browse by: Latest US Patents, China's latest patents, Technical Efficacy Thesaurus, Application Domain, Technology Topic, Popular Technical Reports.
© 2024 PatSnap. All rights reserved.Legal|Privacy policy|Modern Slavery Act Transparency Statement|Sitemap|About US| Contact US: help@patsnap.com