A lithium-ion battery negative electrode with improved high-voltage cycle performance and preparation method thereof
A lithium-ion battery, cycle performance technology, applied in non-aqueous electrolyte battery electrodes, battery electrodes, electrode manufacturing, etc., can solve the problems of large thickness expansion rate, application limitations of high-voltage lithium-ion batteries, short cycle life, etc., to improve Polarization effect, the effect of reducing the risk of lithium precipitation, and improving the cycle performance
- Summary
- Abstract
- Description
- Claims
- Application Information
AI Technical Summary
Problems solved by technology
Method used
Image
Examples
specific Embodiment approach 1
[0022] A lithium-ion battery negative electrode for improving high-voltage cycle performance, comprising a negative electrode current collector and a negative electrode coating. The negative electrode coating includes a long paste layer and a short paste layer. The long paste layer gap is coated on the negative electrode collector. On one surface of the fluid, the short coating layer gap is coated on the other surface of the negative electrode current collector. The long coating layer is composed of the negative electrode main material, the high specific surface area conductive agent, CMC and SBR in accordance with 96.1%-97.3 %: 0.5% to 1.0%: 1.2% to 1.5%: 1.0% to 1.4% by mass, the short coating paste layer is composed of the negative electrode main material, silicon carbon, CMC and SBR in accordance with 96.1% to 97.3%: 0.5% ~1.0%: 1.2%~1.5%: 1.0%~1.4% mass percentage composition.
[0023] Further, the specific surface area of the high specific surface area conductive agent ra...
specific Embodiment approach 2
[0025] A preparation method of lithium ion battery negative electrode with improved high-voltage cycle performance includes the following steps:
[0026] Step 1: Disperse 96.1%-97.3% of the main negative electrode material, 0.5%-1.0% high specific surface area conductive agent, 1.2%-1.5% CMC and 1.0%-1.4% SBR in the solvent deionization. A negative electrode slurry A is made in water, and the negative electrode slurry A is coated on the long paste surface of the negative electrode current collector with a coating thickness of 160-250μm;
[0027] Step 2: Disperse the negative main material of 96.1%-97.3% by mass, 0.5%-1.0% silicon carbon, 1.2%-1.5% CMC and 1.0%-1.4% SBR uniformly in solvent deionized water. Negative electrode slurry B, coating the negative electrode slurry B on the short paste surface of the negative electrode current collector with a coating thickness of 160-250μm;
[0028] Step 3: The negative electrode current collector coated with negative electrode slurry A and ...
specific Embodiment approach 3
[0032] In the second embodiment, a method for preparing a negative electrode of a lithium ion battery with improved high-voltage cycle performance is described. In step one: the specific configuration method of the negative electrode slurry A is: (1) the total mass of the CMC 15% to 65% and all of the high specific surface area conductive agents are pre-mixed and uniformly dispersed in the solvent deionized water in advance; (2) Then add 20% to 30% of the total mass of the negative electrode main material and the total mass of the CMC 5%-15%, uniform dispersion; (3) then add 25%-30% of the total mass of the negative electrode main material and 5%-15% of the total mass of the CMC, uniform dispersion; (4) then add the 25%-30% of the total mass of the main material of the negative electrode and 5%-75% of the total mass of the CMC, uniformly dispersed; (5) Then add 10%-30% of the total mass of the negative main material to make the dispersion uniform; 6) In the last step, all the S...
PUM
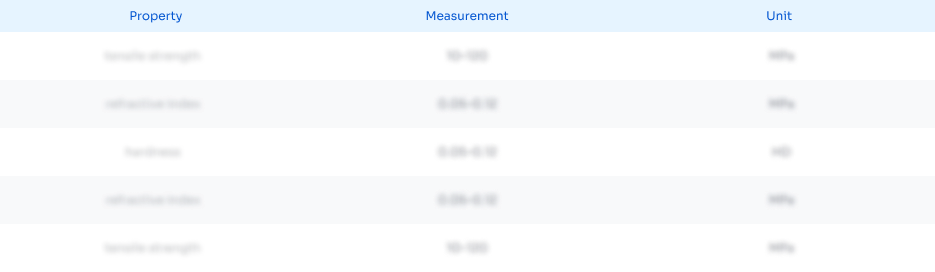
Abstract
Description
Claims
Application Information

- R&D
- Intellectual Property
- Life Sciences
- Materials
- Tech Scout
- Unparalleled Data Quality
- Higher Quality Content
- 60% Fewer Hallucinations
Browse by: Latest US Patents, China's latest patents, Technical Efficacy Thesaurus, Application Domain, Technology Topic, Popular Technical Reports.
© 2025 PatSnap. All rights reserved.Legal|Privacy policy|Modern Slavery Act Transparency Statement|Sitemap|About US| Contact US: help@patsnap.com