Method for avoiding breakout due to extrusion of slab shell during hot width adjustment of continuous casting mold
A technology for continuous casting mold and thermal width adjustment is applied in the field of avoiding steel breakout caused by extrusion of the thermally adjusted billet shell of the continuous casting mold. To achieve the effect of optimizing moving speed, high applicability, and avoiding steel breakout accidents
- Summary
- Abstract
- Description
- Claims
- Application Information
AI Technical Summary
Problems solved by technology
Method used
Image
Examples
Embodiment 1
[0039] 1. For the 1# continuous casting machine of an enterprise, the wide copper plate of the crystallizer is equipped with 6 rows and 3 rows of thermocouples 4;
[0040] 2. For a high-carbon and high-alloy steel grade, it is planned to conduct thermal width adjustment during pouring, and the width of crystallizer 1 is reduced from 1500mm to 1400mm;
[0041] 3. When the pouring speed is 1.3m / min, start to adjust the width;
[0042] 4. At the beginning of widening, the temperature of a row of three thermocouples 4 on the inner arc width surface of crystallizer 1 is 250, 225, and 190°C respectively;
[0043] 5. The temperature of thermocouple 4 remains unchanged at the beginning of width adjustment, and the temperature of the above three thermocouples 4 drops to 215, 192, and 155°C respectively during the width adjustment process;
[0044] 6. The system sends out an abnormal alarm and automatically reduces the speed to 0.6m / min;
[0045] 7. The operator stops the width adjust...
Embodiment 2
[0048] 1. For the 1# continuous casting machine of an enterprise, the wide copper plate of the crystallizer is equipped with 6 rows and 3 rows of thermocouples 4;
[0049] 2. For a certain type of high-strength steel, the No. 1 machine is planned to carry out thermal width adjustment during pouring, and the width of crystallizer 1 is reduced from 1600mm to 1450mm;
[0050] 3. When the pouring speed is 1.1m / min, start to adjust the width;
[0051] 4. Before the width adjustment starts, the temperatures of a row of three thermocouples 4 on the west side of the inner arc width of the crystallizer 1 are 223, 199, and 170°C respectively;
[0052] 5. After the width adjustment starts, the temperatures of the above three thermocouples 4 rise to 260, 235, and 201°C respectively;
[0053] 6. The system sends out an abnormal alarm and automatically reduces the speed to 0.2m / min;
[0054] 7. The operator stopped the width adjustment operation. After the billet came out of the casting m...
PUM
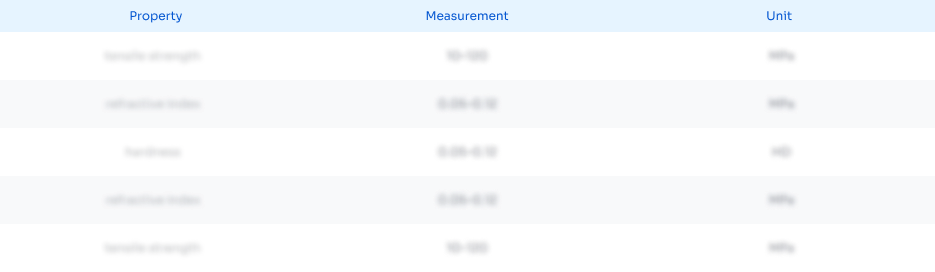
Abstract
Description
Claims
Application Information

- R&D Engineer
- R&D Manager
- IP Professional
- Industry Leading Data Capabilities
- Powerful AI technology
- Patent DNA Extraction
Browse by: Latest US Patents, China's latest patents, Technical Efficacy Thesaurus, Application Domain, Technology Topic, Popular Technical Reports.
© 2024 PatSnap. All rights reserved.Legal|Privacy policy|Modern Slavery Act Transparency Statement|Sitemap|About US| Contact US: help@patsnap.com