Displacement amplifying tuning fork type micro-mechanical gyroscope based on lever effect
A technology of displacement amplification and mechanical gyroscope, which is applied in the direction of gyroscope/steering sensing equipment, gyro effect for speed measurement, instruments, etc., which can solve the problem of small improvement in processing circuit accuracy, low detection accuracy of micro-mechanical gyroscope, and difficulty in displacement detection Large and other problems, to achieve the effect of improving detection accuracy and sensitivity, improving detection sensitivity, and suppressing structural mechanical coupling
- Summary
- Abstract
- Description
- Claims
- Application Information
AI Technical Summary
Problems solved by technology
Method used
Image
Examples
Embodiment Construction
[0037] In order to further understand the content, features and effects of the present invention, the following examples are given, and detailed descriptions are given below with reference to the accompanying drawings.
[0038] The structure of the present invention will be described in detail below in conjunction with the accompanying drawings.
[0039] Such as figure 1 As shown, the lever effect-based displacement amplification tuning fork micromachined gyroscope provided by the embodiment of the present invention includes a glass substrate, metal electrodes, and a MEMS mechanical structure.
[0040] The silicon chip is bonded on the glass substrate, and the silicon chip on the glass substrate is photolithographically etched to form an anchor point, and the glass substrate is photoetched, and sputtered metal is peeled off to form a metal electrode;
[0041] The MEMS mechanical structure released by photolithographic deep etching on the silicon wafer is a fully decoupled ful...
PUM
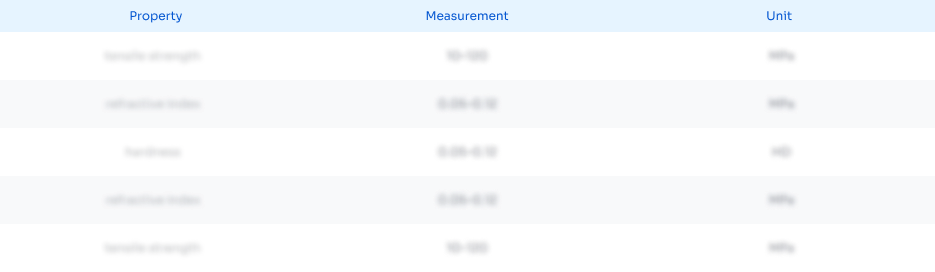
Abstract
Description
Claims
Application Information

- R&D
- Intellectual Property
- Life Sciences
- Materials
- Tech Scout
- Unparalleled Data Quality
- Higher Quality Content
- 60% Fewer Hallucinations
Browse by: Latest US Patents, China's latest patents, Technical Efficacy Thesaurus, Application Domain, Technology Topic, Popular Technical Reports.
© 2025 PatSnap. All rights reserved.Legal|Privacy policy|Modern Slavery Act Transparency Statement|Sitemap|About US| Contact US: help@patsnap.com