Preparation method of high-temperature-resistant biaxially-oriented polypropylene film
A polypropylene film, biaxial stretching technology, applied in the field of plastics, can solve the problems of poor heat resistance and toughness, and achieve the effects of reducing thermal shrinkage, good heat resistance and improving heat resistance.
- Summary
- Abstract
- Description
- Claims
- Application Information
AI Technical Summary
Problems solved by technology
Method used
Examples
Embodiment 1
[0015] A method for preparing a high temperature resistant biaxially stretched polypropylene film, comprising the following steps:
[0016] (1) Add 10 parts by weight of potassium feldspar and 10 parts of basalt fiber to 50 parts of 2% ethanol solution of dodecyltrimethylammonium chloride, stir at 100°C for 10 minutes, and then filter Wash, transfer to a ball mill, grind to particles with a particle size of 50-500nm, add to deionized water, then add 3 parts of sodium hydroxymethyl cellulose, ultrasonically treat at 40°C for 10 minutes, add 15 parts of Na 2 HPO 4 12H 2 O, then use 8% sodium hydroxide solution to adjust its pH to 9, continue ultrasonic treatment for 10 minutes, then transfer to the reaction kettle, react at 150 °C for 10 hours, cool, wash, filter, and dry to obtain hydroxyapatite Stone-coated potassium feldspar and basalt fibers;
[0017] (2) Disperse 20 parts of the product obtained in step (1) into deionized water, then add 4 parts of 8% sodium hydroxide, s...
Embodiment 2
[0023] A method for preparing a high temperature resistant biaxially stretched polypropylene film, comprising the following steps:
[0024] (1) Add 12 parts by weight of potassium feldspar and 13 parts of basalt fiber to 60 parts of 3% dodecyltrimethylammonium chloride ethanol solution, stir at 101°C for 11min, and then filter Wash, transfer to a ball mill, grind to particles with a particle size of 50-500nm, add to deionized water, then add 4 parts of sodium hydroxymethyl cellulose, ultrasonically treat at 45°C for 13 minutes, add 18 parts of Na 2 HPO 4 12H 2 O, then use 10% sodium hydroxide solution to adjust its pH to 9.5, continue ultrasonic treatment for 13 minutes, then transfer to the reactor, react at 153 °C for 11 hours, cool, wash, filter, and dry to obtain hydroxyapatite Stone-coated potassium feldspar and basalt fibers;
[0025] (2) Disperse 23 parts of the product obtained in step (1) into deionized water, then add 5 parts of 10% sodium hydroxide, stir at 300 r...
Embodiment 3
[0031] A method for preparing a high temperature resistant biaxially stretched polypropylene film, comprising the following steps:
[0032] (1) Add 15 parts by weight of potassium feldspar and 15 parts of basalt fiber to 80 parts of 4% dodecyltrimethylammonium chloride ethanol solution, stir at 102°C for 12min, and then filter Wash, transfer to a ball mill, grind to particles with a particle size of 50-500nm, add to deionized water, then add 5 parts of hydroxymethyl cellulose sodium, ultrasonically treat at 50°C for 15 minutes, add 20 parts of Na 2 HPO 4 12H 2 O, then use 12% sodium hydroxide solution to adjust its pH to 10, continue ultrasonic treatment for 15 minutes, then transfer to the reaction kettle, react at 155°C for 12 hours, cool, wash, filter, and dry to obtain hydroxyapatite Stone-coated potassium feldspar and basalt fibers;
[0033] (2) Disperse 25 parts of the product obtained in step (1) into deionized water, then add 6 parts of 12% sodium hydroxide, stir at...
PUM
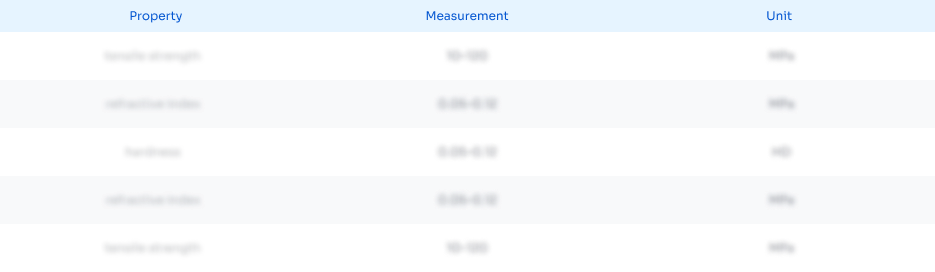
Abstract
Description
Claims
Application Information

- Generate Ideas
- Intellectual Property
- Life Sciences
- Materials
- Tech Scout
- Unparalleled Data Quality
- Higher Quality Content
- 60% Fewer Hallucinations
Browse by: Latest US Patents, China's latest patents, Technical Efficacy Thesaurus, Application Domain, Technology Topic, Popular Technical Reports.
© 2025 PatSnap. All rights reserved.Legal|Privacy policy|Modern Slavery Act Transparency Statement|Sitemap|About US| Contact US: help@patsnap.com