Bamboo wood fiber wallboard and preparation method thereof
A bamboo and wood fiber and wallboard technology, applied in the field of wallboard, can solve problems such as inconvenience, and achieve the effects of facilitating wetting, rapid curing, and improving mechanical properties
- Summary
- Abstract
- Description
- Claims
- Application Information
AI Technical Summary
Problems solved by technology
Method used
Image
Examples
Embodiment 1
[0023] Be the PVC resin of 75 parts by weight, the calcium carbonate powder of 75 parts, the bamboo wood fiber powder of 8 parts, the calcium zinc stabilizer of 5 parts, the AC blowing agent (azodicarbonamide) of 0.8 part, 5 parts The foam regulator, 0.4 parts of stearic acid and 0.6 parts of PE wax are added to the high-speed mixer and mixed at high temperature to 110-130 °C, and then cold-mixed at low temperature to 35-55 °C for discharge. Subsequently, the discharged mixed ingredients are sent to the extruder to complete the extrusion of the base material of the bamboo fiber wallboard. Finally, the extruded substrate is coated with PVC, and the peel strength and bending strength of the finished product are tested.
Embodiment 2
[0025] Be the PVC resin of 75 parts, the calcium carbonate powder of 75 parts, the bamboo wood fiber powder of 8 parts, the calcium zinc stabilizer of 5 parts, the AC blowing agent of 0.8 part, the foaming regulator of 5 parts, the foaming regulator of 0.4 parts by weight ratio 1 part of stearic acid, 0.5 part of PE wax, 0.5 part of PEG with a molecular weight of 6000 and 3 parts of AIM resin are added to a high-speed mixer and mixed at high temperature to 110-130°C, and then cold-mixed at a low temperature to 35-55°C. material. Subsequently, the discharged mixed ingredients are sent to the extruder to complete the extrusion of the base material of the bamboo fiber wallboard. Finally, the extruded substrate is coated with PVC, and the peel strength and bending strength of the finished product are tested.
Embodiment 3
[0027] Be the PVC resin of 75 parts, the calcium carbonate powder of 75 parts, the bamboo wood fiber powder of 8 parts, the calcium zinc stabilizer of 5 parts, the AC blowing agent of 0.8 part, the foaming regulator of 5 parts, the foaming regulator of 0.4 parts by weight ratio 1 part of stearic acid, 0.6 part of PE wax, 0.3 part of PVA fiber and 2 parts of MBS resin are added to a high-speed mixer and mixed at high temperature to 110-130°C, and then cold-mixed at low temperature to 35-55°C and discharged. Subsequently, the discharged mixed ingredients are sent to the extruder to complete the extrusion of the base material of the bamboo fiber wallboard. Finally, the extruded substrate is coated with PVC, and the peel strength and bending strength of the finished product are tested.
PUM
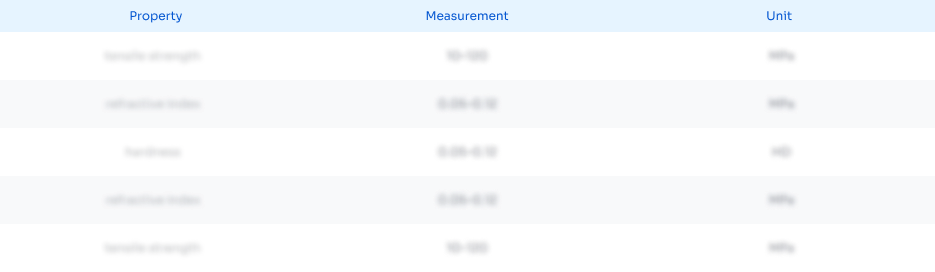
Abstract
Description
Claims
Application Information

- R&D
- Intellectual Property
- Life Sciences
- Materials
- Tech Scout
- Unparalleled Data Quality
- Higher Quality Content
- 60% Fewer Hallucinations
Browse by: Latest US Patents, China's latest patents, Technical Efficacy Thesaurus, Application Domain, Technology Topic, Popular Technical Reports.
© 2025 PatSnap. All rights reserved.Legal|Privacy policy|Modern Slavery Act Transparency Statement|Sitemap|About US| Contact US: help@patsnap.com