High-flame-retardancy foam material for coal wagon blocking
A foamed material, high flame retardant technology, applied in the field of sealing materials, can solve problems such as insufficient flame retardant, scattering, pressure tank explosion, etc., achieve high heat resistance and compressive strength, enhance flame retardant and combine Strength, the effect of strengthening the overall strength
- Summary
- Abstract
- Description
- Claims
- Application Information
AI Technical Summary
Problems solved by technology
Method used
Examples
Embodiment 1
[0025] A high flame retardant foaming agent for coal wagon skin sealing, the foaming agent is composed of three components A, B, and C, and component A consists of 65g of 4063 polyether polyol, 7g of microporous silicon Calcium trisilicate, 10g magnesium trisilicate, 10g cyclopentane, 3.5g mixture of pentamethyldiethylenetriamine and potassium isooctanoate, 2g polyoxyethylene ether of nonylphenol, 5g tetrakis(2-chloroethyl ) Ethylene diphosphate; B component is the prepolymer of isocyanate and polyether polyol of 85g; The preparation method of the prepolymer of isocyanate and polyether polyol is according to mass ratio 2 of isocyanate and polyether polyol: 1 Mix and mix, heat up to 80°C, stir and keep warm for 1 hour; component C is 20g of glacial acetic acid.
[0026] The concrete preparation method of whipping agent is:
[0027] 1) Make component A: first add 4063 polyether polyol into the reaction kettle, start the stirrer, keep the temperature at 80°C, add microporous cal...
Embodiment 2
[0031] A high flame-retardant foaming agent for coal wagon skin sealing, the foaming agent is composed of three components A, B, and C, and the A component is composed of 80g of polyester polyol, 12g of microporous silicic acid Calcium, 6g magnesium trisilicate, 15g methylene chloride, 4g mixture of dimethylcyclohexylamine and dibutyltin dilaurate, 5g polyoxyethylene ether of nonylphenol, 10g tris(2-chloropropyl) phosphate ; B component is the prepolymer of the isocyanate and polyether polyol of 100g; ℃, stirred and kept for 2 hours; C component is 10g of glacial acetic acid.
[0032] The concrete preparation method of whipping agent is:
[0033] 1) To make component A: first add polyester polyol into the reaction kettle, start the agitator, keep the temperature at 80°C, add microporous calcium silicate and magnesium trisilicate and stir for 30 minutes, then add dimethylcyclohexylamine Mixture with dibutyltin dilaurate, polyoxyethylene ether of nonylphenol, three (2-chloropr...
Embodiment 3
[0037] A high flame-retardant foaming agent for coal wagon skin sealing, said foaming agent is composed of three components A, B, and C, and component A consists of 60g of polyester polyol, 8g of microporous silicic acid Calcium, 8g magnesium trisilicate, 20g HCFC-141b, 3g mixture of dimethylcyclohexylamine and dibutyltin dilaurate, 2g polyoxyethylene ether of nonylphenol, 10g tetrakis (2-chloroethyl) diethylene Ethyl ether diphosphate; B component is the prepolymer of 90g isocyanate and polyether polyol; the preparation method of the prepolymer of isocyanate and polyether polyol is according to mass ratio 1:1.5 of isocyanate and polyether polyol Mix and mix, heat up to 80°C, stir and keep warm for 1.5 hours; component C is 25g of glacial acetic acid.
[0038] The concrete preparation method of whipping agent is:
[0039] 1) Make component A: firstly add polyester polyol into the reaction kettle, start the stirrer, keep the temperature at 80°C, add microporous calcium silicate ...
PUM
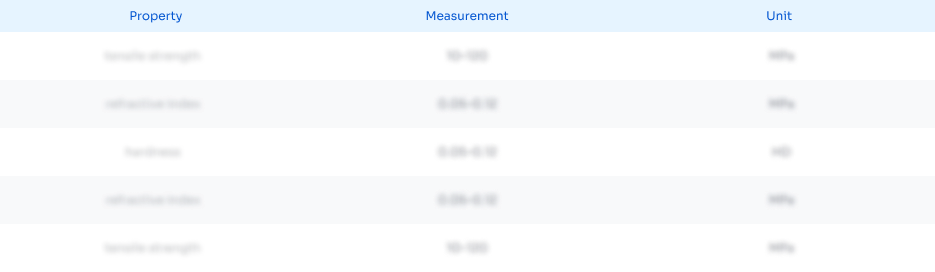
Abstract
Description
Claims
Application Information

- Generate Ideas
- Intellectual Property
- Life Sciences
- Materials
- Tech Scout
- Unparalleled Data Quality
- Higher Quality Content
- 60% Fewer Hallucinations
Browse by: Latest US Patents, China's latest patents, Technical Efficacy Thesaurus, Application Domain, Technology Topic, Popular Technical Reports.
© 2025 PatSnap. All rights reserved.Legal|Privacy policy|Modern Slavery Act Transparency Statement|Sitemap|About US| Contact US: help@patsnap.com