Rotary heat transfer experiment system and method for turbine blade cooling performance test
A technology of cooling performance and turbine blades, which is applied in the field of rotating heat transfer experimental systems to achieve intelligent control, powerful functions and save experimental time.
- Summary
- Abstract
- Description
- Claims
- Application Information
AI Technical Summary
Problems solved by technology
Method used
Image
Examples
Embodiment Construction
[0035] The present invention will be described in further detail below in conjunction with the accompanying drawings and embodiments.
[0036] refer to Figure 1 ~ Figure 4 The present invention provides a rotary heat transfer experimental system for testing the cooling performance of turbine blades, including a static air supply system, a rotary experimental test platform and a control system.
[0037] Among them, the static air supply system includes an air pump 1, a steady flow tank 2, a temperature control device 17, a three-way solenoid valve 3, a flow meter 4, a pressure gauge 5, and corresponding static connection pipelines; the rotating experiment test platform includes a motor 16, a rotating speed Sensor, transmission gear box 15, support platform 14, circular test bench 12, experimental test section 10, corresponding rotating connection pipeline and high-speed thermal imaging system; high-speed thermal imaging system includes high-speed thermal imaging device 21 and ...
PUM
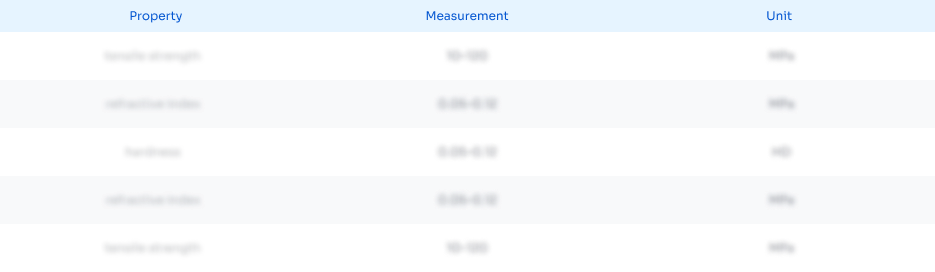
Abstract
Description
Claims
Application Information

- R&D Engineer
- R&D Manager
- IP Professional
- Industry Leading Data Capabilities
- Powerful AI technology
- Patent DNA Extraction
Browse by: Latest US Patents, China's latest patents, Technical Efficacy Thesaurus, Application Domain, Technology Topic, Popular Technical Reports.
© 2024 PatSnap. All rights reserved.Legal|Privacy policy|Modern Slavery Act Transparency Statement|Sitemap|About US| Contact US: help@patsnap.com