Main shaft front and back welding process based on welding main driving system
A drive system and welding process technology, applied in welding equipment, welding accessories, manufacturing tools, etc., can solve the problems of large welding current loss, affecting the quality of a weld forming, and the weight of the welding workpiece itself, and achieve the effect of high verticality
- Summary
- Abstract
- Description
- Claims
- Application Information
AI Technical Summary
Problems solved by technology
Method used
Image
Examples
Embodiment
[0079] Embodiment: refer to attached Figure 1-11 , 4a, 4a 1, 4a 2, 4b, 4b 1, 4b2, 5a, 5b, as shown, the front and back welding process of the main shaft based on the welding total drive system includes the following process steps:
[0080] Front side welding
[0081] S1: Pre-spelling
[0082] Put the large flange 3 and small flange 2 on the main shaft 1 according to the requirements of the drawings, and fix them by spot welding on the non-groove side;
[0083] S2: warm up
[0084] Preheat the spot-welded spindle 1 in an oven at 230°C and keep it warm for 1 hour until the workpiece is at 150-200°C;
[0085] S3: Spindle 190 degree rotation installation
[0086] Refer to attached Figure 8 , 10 As shown, hoist the preheated main shaft 1 and armrest shaft to the welding workstation, and fix the main shaft 1 vertically through the 90-degree fixing device;
[0087] The 90-degree fixing device includes a vertical pile 11, an automatic compactor 10 fixed on the vertical pile 1...
PUM
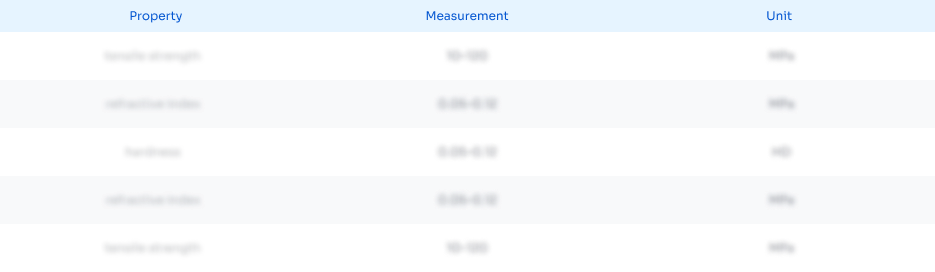
Abstract
Description
Claims
Application Information

- Generate Ideas
- Intellectual Property
- Life Sciences
- Materials
- Tech Scout
- Unparalleled Data Quality
- Higher Quality Content
- 60% Fewer Hallucinations
Browse by: Latest US Patents, China's latest patents, Technical Efficacy Thesaurus, Application Domain, Technology Topic, Popular Technical Reports.
© 2025 PatSnap. All rights reserved.Legal|Privacy policy|Modern Slavery Act Transparency Statement|Sitemap|About US| Contact US: help@patsnap.com