Metal surface nitriding technology
A technology for metal surfaces and metal workpieces, which is applied in the field of surface chemical treatment, can solve problems such as limited effects, and achieve the effects of improved effects, fast cleaning effects, and high reaction efficiency
- Summary
- Abstract
- Description
- Claims
- Application Information
AI Technical Summary
Problems solved by technology
Method used
Image
Examples
Embodiment 1
[0047] A process for nitriding a metal surface, including a metal workpiece to be processed, the processing of the workpiece includes the following steps:
[0048] 1) Rinse the workpiece with water containing detergent, and then rinse the workpiece with 100°C water after rinsing with clean water;
[0049] 2) Put the oil-removed workpiece in the pool for ultrasonic cleaning, the cleaning vibration frequency is 80KHz, the power density is set at 0.6W / C, and the ultrasonic cleaning time is 8min;
[0050] 3) Preheat the workpiece to 300°C, and the preheating time is 6 minutes;
[0051] 4) Place the workpiece in the nitriding furnace containing Li ion base salt, then extract the air in the nitriding furnace, and refill the mixed gas into the nitriding furnace;
[0052] 5) Place the workpiece in a nitriding furnace with a base salt containing Li ions, raise the nitriding furnace to 520°C, and nitriding time is 80 minutes;
[0053] 6) Add solid sodium peroxide to the base salt, and t...
Embodiment 2
[0067] A process for nitriding a metal surface, including a metal workpiece to be processed, the processing of the workpiece includes the following steps:
[0068] 1) Rinse the workpiece with water containing detergent, and then rinse the workpiece with 100°C water after rinsing with clean water;
[0069] 2) Put the oil-removed workpiece in the pool for ultrasonic cleaning, the cleaning vibration frequency is 120KHz, the power density is set at 0.8W / C, and the ultrasonic cleaning time is 12min;
[0070] 3) Preheat the workpiece to 355°C, and the preheating time is 15 minutes;
[0071] 4) Put the workpiece in the nitriding furnace containing Li ion base salt, then extract the air in the nitriding furnace, and refill the mixed gas into the nitriding furnace
[0072] 5) Place the workpiece in a nitriding furnace with a base salt containing Li ions, raise the nitriding furnace to 550°C, and nitriding time is 93 minutes;
[0073] 6) Add solid sodium peroxide to the base salt, and...
Embodiment 3
[0087] A process for nitriding a metal surface, including a metal workpiece to be processed, the processing of the workpiece includes the following steps:
[0088] 1) Rinse the workpiece with water containing detergent, and then rinse the workpiece with 100°C water after rinsing with clean water;
[0089] 2) Put the oil-removed workpiece in the pool for ultrasonic cleaning, the cleaning vibration frequency is 160KHz, the power density is set at 1.0W / C, and the ultrasonic cleaning time is 15min;
[0090] 3) Preheat the workpiece to 385°C, and the preheating time is 25 minutes;
[0091] 4) Place the workpiece in the nitriding furnace containing Li ion base salt, then extract the air in the nitriding furnace, and refill the mixed gas into the nitriding furnace;
[0092] 5) Place the workpiece in a nitriding furnace with a base salt containing Li ions, raise the nitriding furnace to 580°C, and nitriding time is 100min;
[0093] 6) Add solid sodium peroxide to the base salt, and ...
PUM
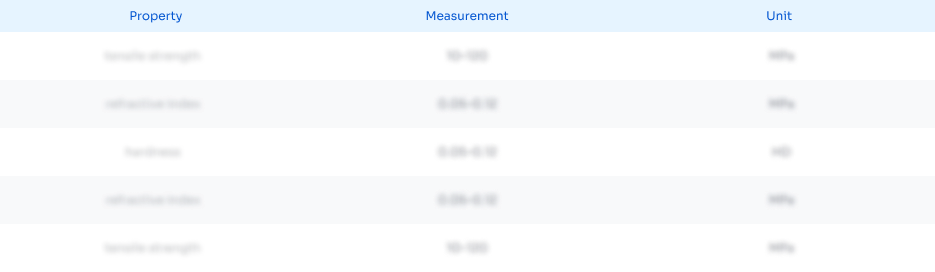
Abstract
Description
Claims
Application Information

- R&D
- Intellectual Property
- Life Sciences
- Materials
- Tech Scout
- Unparalleled Data Quality
- Higher Quality Content
- 60% Fewer Hallucinations
Browse by: Latest US Patents, China's latest patents, Technical Efficacy Thesaurus, Application Domain, Technology Topic, Popular Technical Reports.
© 2025 PatSnap. All rights reserved.Legal|Privacy policy|Modern Slavery Act Transparency Statement|Sitemap|About US| Contact US: help@patsnap.com