Method for preparing biphenyl derivative by using microchannel continuous flow reactor
A microchannel and reactor technology, applied in chemical instruments and methods, chemical/physical/physical chemical reactors, preparation of organic compounds, etc., can solve the problems of runaway reaction, slow reaction or even stop, low heat transfer efficiency, etc. , to achieve the effect of reducing the reaction time, shortening the diffusion distance, and increasing the reaction rate
- Summary
- Abstract
- Description
- Claims
- Application Information
AI Technical Summary
Problems solved by technology
Method used
Image
Examples
experiment example 1
[0069] Experimental Example 1 Preparation of Grignard Reagent
[0070] Preparation of Grignard Reagent for 4-Chloro-o-xylene : According to the standard operation of Grignard reagent preparation, a small amount of 4-chloro-o-xylene and solvent are added dropwise to the activated magnesium chips under nitrogen gas, and a small amount of iodine is added as an initiator and heated to initiate. After initiation, the remaining 4-chloro-o-xylene and solvent were added dropwise and kept in a reflux state, and continued to reflux for 2 hours after the dropwise addition was completed. Calibrate format reagent, adjust the concentration to 2.5mol / L. record as 1 # format reagents.
[0071] Preparation of Grignard reagent for p-chlorotoluene : According to the standard operation of the Grignard reagent preparation, a small amount of p-chlorotoluene and solvent are added dropwise to the activated magnesium chips under nitrogen conditions, and a small amount of iodine is added as an in...
Embodiment 1
[0074] Example 1 Preparation of 3,3',4,4'-tetramethylbiphenyl
[0075] Typically, with figure 1 The process schematic diagram shown in is a route to prepare biphenyl compounds. The continuous flow reactor is a microchannel continuous flow reactor (Corning SiC-G1), and the internal structure of the microchannel continuous flow reactor is a heart-shaped channel. The diameter of the microchannel is 100 μm.
[0076] Preparation method 1
[0077] Take 10mol of calibrated 1 # The THF solution of Grignard reagent is used as material A solution, take 10mol of 4-chloro-o-xylene, 30mmol of NiCl 2 , PPh of 60mmol 3 Mix and heat to 80°C, and heat for 30 minutes, as material B solution;
[0078] Then through the metering pump, A and B are respectively entered into the preheating module of the continuous flow reactor according to the molar ratio of 1:1, and the temperature of the preheating module is controlled to 120°C;
[0079]After passing through the preheating module, solution...
Embodiment 2
[0083] Example 2 Preparation of 4,4'-dimethylbiphenyl
[0084] The preparation process is as figure 1 The process shown in Fig.
[0085] Take 10mol of calibrated 2 # The THF solution of Grignard reagent is used as material A solution, take 10mol of p-chlorotoluene, 20mmol of NiCl 2 , 40mmol of PPh 3 Mix and heat to 80°C, and heat for 30 minutes, as material B solution;
[0086] Then through the metering pump, A and B are respectively entered into the continuous flow reactor preheating module according to the molar ratio of 1:1, and the temperature of the preheating module is controlled to 140 °C; the continuous flow reactor is a microchannel continuous flow reactor (Corning SiC-G1) , the internal structure of the microchannel continuous flow reactor is a heart-shaped channel;
[0087] After passing through the preheating module, solutions A and B enter the mixed reaction module, the reaction temperature is set at 140°C (the first 80% module) + 175°C (the last 20% module),...
PUM
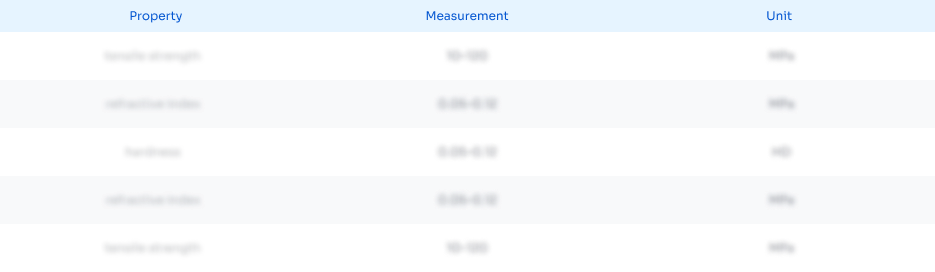
Abstract
Description
Claims
Application Information

- R&D
- Intellectual Property
- Life Sciences
- Materials
- Tech Scout
- Unparalleled Data Quality
- Higher Quality Content
- 60% Fewer Hallucinations
Browse by: Latest US Patents, China's latest patents, Technical Efficacy Thesaurus, Application Domain, Technology Topic, Popular Technical Reports.
© 2025 PatSnap. All rights reserved.Legal|Privacy policy|Modern Slavery Act Transparency Statement|Sitemap|About US| Contact US: help@patsnap.com