High-compactness electric static pressure actuator for robot joints
A technology of robot joints and actuators, which is applied in the field of machinery, can solve problems such as increasing the installation space and overall weight of robot equipment, clogging of servo valve spray baffles, poor load impact resistance, etc., to eliminate easy pollution and clogging, and improve sealing Reliability, the effect of small system heat generation
- Summary
- Abstract
- Description
- Claims
- Application Information
AI Technical Summary
Problems solved by technology
Method used
Image
Examples
Embodiment Construction
[0025] The present invention will be further described in conjunction with the accompanying drawings.
[0026] Such as image 3 , 4 As shown, a high-compact electrostatic actuator 23 for a robot joint includes an integrated housing 1, a knee joint connection block 2, a hip joint connection block 3, a motor pump assembly, an actuator assembly, and hydraulic accessories;
[0027] Such as figure 1 As shown, the knee joint connection block 2 and the hip joint connection block 3 are respectively installed on both ends of the integrated housing 1 by screws. The parts 19 are connected, and the hip joint connection block 3 is provided with a hip joint connection port 22, which is connected with the hip joint part 20 of the robot; the motor pump assembly and the actuator assembly are installed in the integrated housing 1, and the hydraulic accessories are installed in the hip joint. In the joint part connection block 3; the motor pump assembly provides power for the movement of the ...
PUM
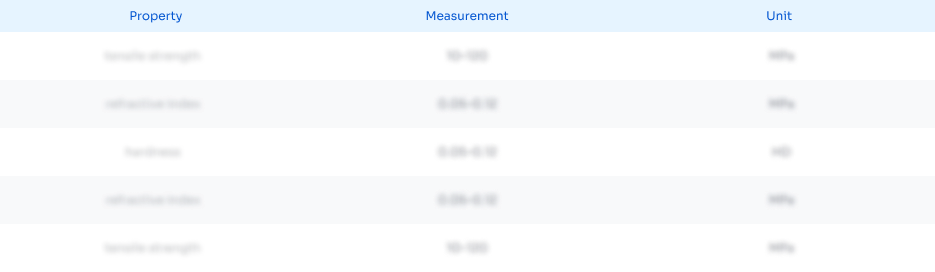
Abstract
Description
Claims
Application Information

- Generate Ideas
- Intellectual Property
- Life Sciences
- Materials
- Tech Scout
- Unparalleled Data Quality
- Higher Quality Content
- 60% Fewer Hallucinations
Browse by: Latest US Patents, China's latest patents, Technical Efficacy Thesaurus, Application Domain, Technology Topic, Popular Technical Reports.
© 2025 PatSnap. All rights reserved.Legal|Privacy policy|Modern Slavery Act Transparency Statement|Sitemap|About US| Contact US: help@patsnap.com