Metal alloy catalyst for dehydrogenation of light alkane as well as preparation method and application of metal alloy catalyst
A technology of low-carbon alkanes and metal alloys, applied in catalyst activation/preparation, metal/metal oxide/metal hydroxide catalysts, hydrocarbons, etc., can solve large particle size, poor dispersion, uneven composition and structure and other problems, to achieve the effect of high selectivity, good regeneration performance and slow deactivation
- Summary
- Abstract
- Description
- Claims
- Application Information
AI Technical Summary
Problems solved by technology
Method used
Image
Examples
Embodiment 1
[0027] Weigh 5.00 g of aluminum oxide (Al 2 o 3 ) loaded with 0.037 g Sn compound (stannous octoate). After immersing in stannous octoate solution at room temperature for 6 h, dry at 120 °C for 8 h, and bake at 500 °C for 4 h. A compound (PtCl 4 ·5H 2 O), impregnated at room temperature for 6 h, dried at 120 °C for 12 h, and calcined at 550 °C for 4 h to obtain Pt-Sn / Al 2 o 3 catalyst. In a fixed-bed tubular reactor filled with 1 g of the catalyst prepared in Example 1, the reactant is propane, the reaction temperature is 550 ° C, the reaction pressure is normal pressure, and the propane weight hourly space velocity is 8 h -1 , under the condition that the ratio of hydrogen to hydrocarbon is 1, the conversion rate of propane is 38%, and the selectivity of propylene is 99.3%.
Embodiment 2
[0029] Weigh 5.00 g of silicon dioxide (SiO 2 ) loaded with 0.042 g Ge compound (Ge(Ph) 4 ). Impregnated Ge(Ph) at room temperature 4 After 6 h, the solution was dried at 120 °C for 8 h, and then calcined at 500 °C for 4 h. A compound (H 2 PtCl 4 ), impregnated at room temperature for 6 h, dried at 120 °C for 12 h, and calcined at 520 °C for 4 h to obtain Pt-Ge / SiO 2 catalyst. In a fixed-bed tubular reactor filled with 1 g of the catalyst prepared in Example 2, the reactant is propane, the reaction temperature is 550 ° C, the reaction pressure is normal pressure, and the propane weight hourly space velocity is 5 h -1 , under the condition that the ratio of hydrogen to hydrocarbon is 1, the conversion rate of propane is 37.5%, and the selectivity of propylene is 98%.
Embodiment 3
[0031] Weigh 3.00 g magnesium oxide (MgO) loaded with 0.022 g Ga compound (Ga(TMHD) 3 ). Room temperature impregnated Ga(TMHD) 3 After 6 h, the solution was dried at 120 °C for 8 h, and then calcined at 500 °C for 4 h. 0.061 g Pt compound (K 2 PtCl 4 ), impregnated at room temperature for 6 h, dried at 120 °C for 12 h, and calcined at 540 °C for 4 h to prepare the Pt-Ga / MgO catalyst. In a fixed-bed tubular reactor filled with 1 g of the catalyst prepared in Example 3, the reactant is propane, the reaction temperature is 550 ° C, the reaction pressure is normal pressure, and the propane weight hourly space velocity is 6 h -1 , under the condition that the ratio of hydrogen to hydrocarbon is 1, the conversion rate of propane is 37%, and the selectivity of propylene is 99%.
PUM
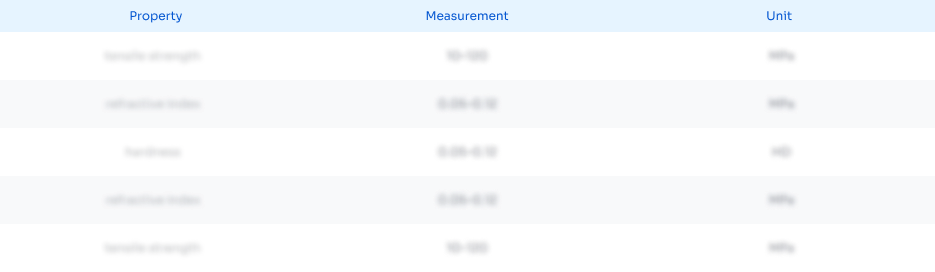
Abstract
Description
Claims
Application Information

- R&D Engineer
- R&D Manager
- IP Professional
- Industry Leading Data Capabilities
- Powerful AI technology
- Patent DNA Extraction
Browse by: Latest US Patents, China's latest patents, Technical Efficacy Thesaurus, Application Domain, Technology Topic, Popular Technical Reports.
© 2024 PatSnap. All rights reserved.Legal|Privacy policy|Modern Slavery Act Transparency Statement|Sitemap|About US| Contact US: help@patsnap.com