Full-speed range position sensorless improvement control method of large-power hub motor
A technology of in-wheel motor and control method, which is applied in motor control, motor generator control, AC motor control and other directions, can solve the problems of excessive occupation of software and hardware resources of the control system, affecting the normal driving of the vehicle, and unable to control the motor normally, etc. Save software and hardware resources, improve the effect significantly, and reduce the effect of the operating range
- Summary
- Abstract
- Description
- Claims
- Application Information
AI Technical Summary
Problems solved by technology
Method used
Image
Examples
Embodiment 1
[0038] see Figure 1-10 , the present invention provides a kind of technical scheme:
[0039] An improved control method without a position sensor in the full speed range of a high-power in-wheel motor, such as figure 1 shown, including the following steps:
[0040] S1: Establish mathematical models in different coordinate systems, analyze the mathematical models of PMSM in different coordinate systems, and combine the control requirements of the in-wheel motors of electric drive armored vehicles, take the torque value as the control amount, and combine with SVPWM technology to build a system based on MTPA and In-wheel motor vector control system for field weakening control to achieve high-performance control of the motor; including the following steps:
[0041] A: Mathematical modeling of PMSM in a-b-c coordinate system;
[0042] B: Mathematical modeling of PMSM in α-β and d-q coordinate systems;
[0043] S2: Build a position sensorless identification system combined with...
PUM
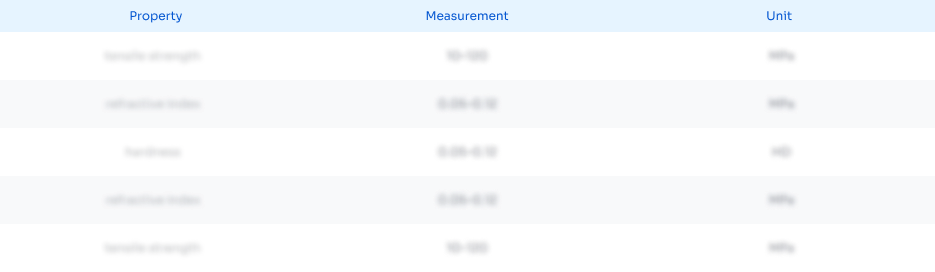
Abstract
Description
Claims
Application Information

- Generate Ideas
- Intellectual Property
- Life Sciences
- Materials
- Tech Scout
- Unparalleled Data Quality
- Higher Quality Content
- 60% Fewer Hallucinations
Browse by: Latest US Patents, China's latest patents, Technical Efficacy Thesaurus, Application Domain, Technology Topic, Popular Technical Reports.
© 2025 PatSnap. All rights reserved.Legal|Privacy policy|Modern Slavery Act Transparency Statement|Sitemap|About US| Contact US: help@patsnap.com