Electric spindle system provided with oscillating heat pipe and heat-structure coupling characteristic modeling method thereof
A technology of oscillating heat pipes and modeling methods, applied in the field of machinery, can solve problems such as thermal deformation, research on electric spindle systems, failure to predict the life of parts such as electric spindle bearings, etc., to reduce errors, ensure modeling accuracy, and good heat transfer performance effect
- Summary
- Abstract
- Description
- Claims
- Application Information
AI Technical Summary
Problems solved by technology
Method used
Image
Examples
Embodiment Construction
[0050] Hereinafter, preferred embodiments of the present invention will be described in detail with reference to the accompanying drawings. It should be understood that the preferred embodiments are only for illustrating the present invention, but not for limiting the protection scope of the present invention.
[0051] The invention provides an electric spindle system configured with an oscillating heat pipe, such as figure 1 As shown, it includes a main shaft housing 1, an encoder 2, a motor stator 3, and a motor rotor 4. It also includes a main shaft 5, which is arranged inside the main shaft housing 1, and a front bearing 6 and a rear bearing 7 to realize the connection between the main shaft 5 and the main shaft housing. 1 is fixed, the main shaft 5 is connected with the motor rotor 4 to realize the rotation of the main shaft 5, a cooling water jacket 8 is arranged on the outer surface of the motor stator 3, and an oscillating heat pipe is arranged inside the main shaft 5 ...
PUM
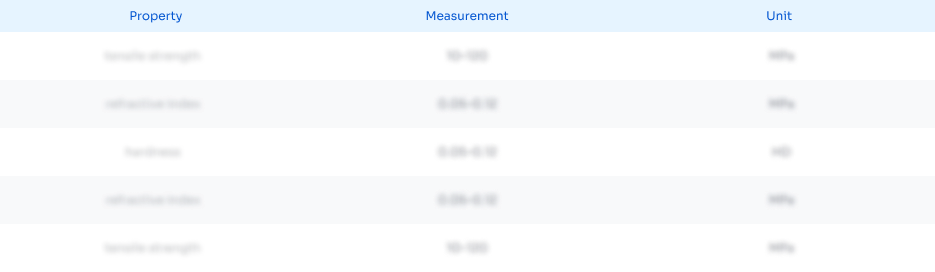
Abstract
Description
Claims
Application Information

- R&D Engineer
- R&D Manager
- IP Professional
- Industry Leading Data Capabilities
- Powerful AI technology
- Patent DNA Extraction
Browse by: Latest US Patents, China's latest patents, Technical Efficacy Thesaurus, Application Domain, Technology Topic, Popular Technical Reports.
© 2024 PatSnap. All rights reserved.Legal|Privacy policy|Modern Slavery Act Transparency Statement|Sitemap|About US| Contact US: help@patsnap.com